June 13, 2021
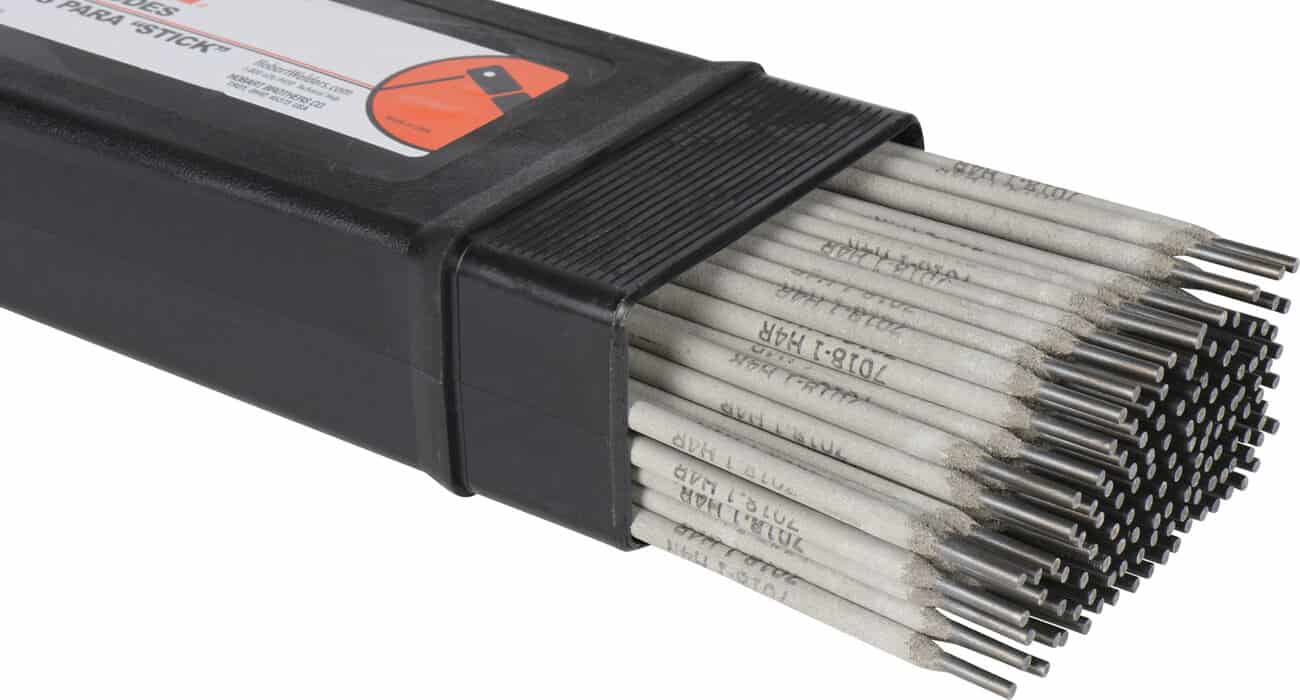
The 7018 welding electrode is very popular for its versatility and flexibility on various types of welding purposes. This rod is always referred to as the “low-hydrogen electrode” with the moisture outer coating that is very useful to create a strong crack-resistant weld. However, the only tricky thing when working with the 7018 is its storage. So, let’s dive right into more details about the 7018 welding rod and other things that you might not know about this rod.
Features & Characteristics of E7018 Welding Rod
The E7018 is a versatile welding rod, frequently used for low and medium carbon steel welding. Also referred to as a “low-hydrogen” rod, this electrode has a flux coating with a very low hydrogen content, allowing a minimal amount of hydrogen into the weld puddle. The molten weld beads are protected from contamination, moisture, and hydrogen in the atmosphere by the iron-containing powder of the flux compound. Consequently, the low hydrogen quantity reaching the weld deposit results in very ductile and robust welds with x-ray quality, withstanding about 70,000 Ibs. Per square inch.
This is a user-friendly electrode (much more so than, for example, the E6011 and E6010), generating a stable arc that provides low to medium penetration while remaining quiet and producing minimal amounts of spatter. Moreover, it offers a high deposition rate and efficiency, is suitable for all welding positions and is compatible with AC as well as DC welders. The slag is slightly heavy yet easily removable, leaving behind a finish consisting of smooth beads with distinct ripples.
7018 Rod Applications
The 7018 or officially “the E7018 welding rod” is a medium-penetration “fill-freeze” electrode designed to weld high-tensile carbon-steel materials.
It is very suitable to use on the metals that are very difficult to be welded as the low-hydrogen flux coating that been coated on the 7018 rods is designed to make the welding process more smoothly and effectively for those hard-to-work metals. The E7018 welding rod is highly regarded especially in structural welding due to its robust weld qualities and is commonly used in the construction of high-rise buildings, bridges, shopping malls, dams, and other highly-strengthened structures. Moreover, E7018 welding rods are easy to use with smooth weld results.
Unlike most “fill-freeze” welding rods that use direct or straight polarity DC current, the E7018 is identified as a reverse polarity DC or DC+ electrode. However, the E7018 possesses a flux coating that is designed to work with AC or alternating current as well. Moreover, the same flux coating often leads to the classification of the E7018 as “low-hydrogen” electrode.
Due to its strong, crack-resistant welds and its aesthetically pleasing finish, E7018 is perfectly suitable and widely used for structural welding. Other common areas of application are:
- Pipe welding
- Welding of pressure vessels
- Welding boilers
- Heavy-duty equipment
- Ship hull construction
- General manufacturing and maintenance labor
What Do the Numbers Mean on a 7018 Welding Rod?
The E7018 welding rod is one of the several electrode types with AWS designation. The AWS assigns four or five digits after the letter. In this designation system, the first two or three digits indicate the tensile strength of the welded material, which is measured in kpi or kilo-pounds per square inch.
- 70: In E7018, the 70 means 70,000 psi or 70 kpi.
- 1: The third digit indicates the welding position. No. 1 denotes all positions welding purposes.
- 8: The last digit of “8” indicates the coating type or materials, penetration, and the types of current that can be employed for the electrode. For E7018 welding rods, the “8” is indicative of low-hydrogen flux mixed with potassium and iron powder compounds. The number “8” likewise indicates its medium penetration quality. Moreover, this number also denotes that this electrode works on reverse polarity DC current, DCEP and AC.
Some electrodes like the E7018 have additional requirements, and these requirements are denoted by a suffix in its designation (i.e., E7018-1). The suffix “-1” indicates increased toughness or ductility; “-M” for military requirements; H4, H8, and H16 are indicative of diffusible hydrogen limits in mL/100 grams (e.g., H8 = 8 mL/100 grams). In addition to these requirements, the suffix can also signify the presence of a particular alloy in a low-alloy steel-coated electrode.
Tips on How To Weld E7018 Welding Rod
Welding with E7018 electrode can be tricky. The E7018 is a very versatile electrode as it deposits a significant amount of materials to create a very strong weld, but it can quickly solidify as well. In order to create an optimum weld, you should follow these guidelines:
- Keep your welding arc tight and concentrate the heat at the weld joint. Wider arc results in a wider weld. The wider weld may distort the workpiece and dislodge the filler material where it’s not needed.
- Keep the distance between the tip of the electrodes and the workpiece during the welding process. The consumable electrode gets shorter as the welding progresses and thus the distance between the rod and workpiece should be maintained soon after the arc was created.
- Keep practicing. As the old adage states, “practice makes perfect.” A lot of practice builds welding skill and confidence.
Additional Tips
7018 Amperage Settings
There is a recommended amperage for every corresponding rod diameter size or for the thickness of steel you plan to weld with the 7018 rods.
You can refer to the rod manufacturer’s manuals for setting up the accurate amps. If, for whatever reason, there is no such recommendation, the prevailing general rule for amperage as listed below.
In general rules of thumb, you can increase current up to 30 amps per 1/32 inch rod diameter. However, the thickness of steel is the additional factor you needed to take into consideration too.
- When using a 3/32-inch diameter rod is that you will need to use 50 amps on 1/16-inch steel thickness and around 90 amps on the ⅛-inch thickness of steel.
- You will need to set the amps much higher for the bigger rods. For 5/32-inch diameter rod, you can set the current at 120 amps for welding the 1/4-inch steel.
- With the same 5/32-inch diameter rod, you can increase the current up to 180 for welding the 3/8-inch steel.
- For the 3/16-inch diameter rod, the current is at 150 amps for welding the 3/8-inch steel.
In conclusion, These amperage recommendations may vary from one manufacturer to another. The best practice for identifying the correct amp’s volume is through the observation of the conditions of the welding rod and the results of the welding. Commonly, the maximum currents you can use with the 7018 rods is up to 225 amps.
What If The Current Is Too Low?
If the amp is too low, you will have a tough time to melt the rod and the joint effectively. The rod head will stick to the surface of the welding object occasionally during the welding process. And the molten puddle is that sufficiently penetrate through the metal to form the two metal in one piece.
What If The Current Is Too High?
If the current is too high, the welding “keyhole” during the welding process is too large and easily melt through the metal and leaving a broken hole on the steel. The welding rod will become melting-red up to if you set the current too high.
E7018 Welding Rod Care
It is of utmost importance that the E7018 are appropriately stored in a moisture-free environment as moisture can easily degrade the low-hydrogen flux coating of the electrode. When the low-hydrogen electrode flux absorbs moisture, the resulting arc tends to pop and spit. Moreover, the weld becomes weak and porous. Shielding the E7018 welding rod from moisture can be achieved by using specialized rod ovens. Improvised rod ovens made from defunct, old refrigerators can be used by simply adding a high-wattage lamp inside; but this is not widely recommended.
Welding rods exposed to moisture for a considerable amount of time should be re-baked at around 371℃ to 427℃ (700℉ to 800℉). Moreover, the E7018 welding rods should be handled with care as the flux coating can break-off from the rod. Damage rod tips can produce long electric arcs. However, if the flux is damaged along the length of the flux coating, the welding rod needs to be replaced before the damaged part or should be replaced completely.