August 13, 2021
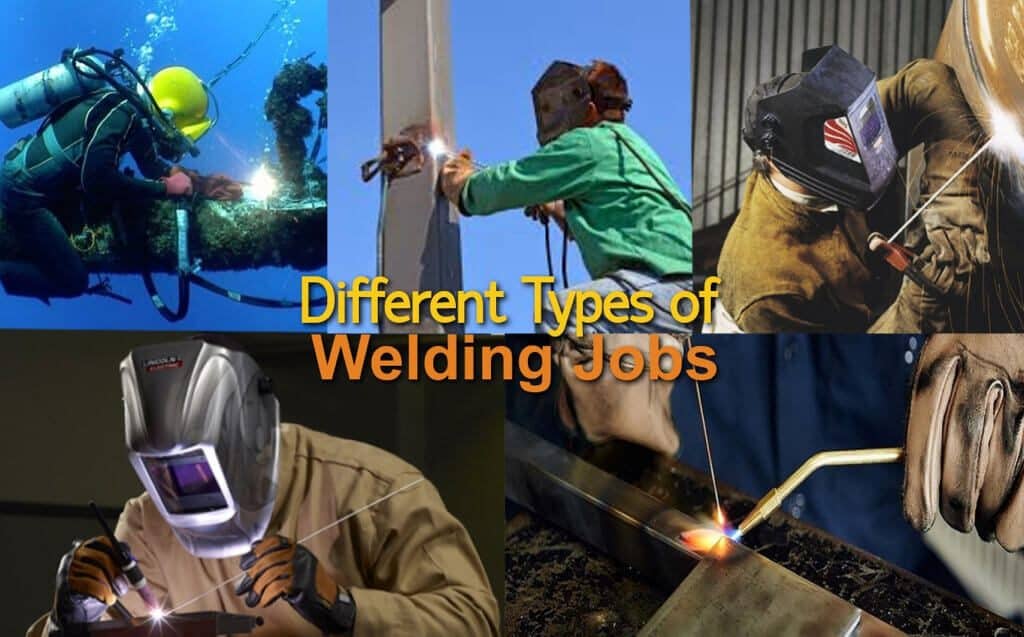
Welding is a standard process both in the manufacturing and construction industries. For a specific application, there are well over 100 different welding processes. Welders are employed in automobile, shipbuilding and aerospace industries. Not only that, but they also join rafters and beams in residential and commercial construction. Laying of pipelines and working to build and maintain power plants and refineries are also some of their tasks. At times, many welders are certified in one or more welding techniques such as MIG welding, stick welding, and TIG welding.
Since the industrial revolution, the technological advancements of mankind have been moving at an unprecedentedly brisk pace. The different human industries likewise have manifested great innovations. With the introduction, for example, of steel as a construction material, the different fabrication methods and techniques have been significantly developed, and because of the limited natural sources of mineral ores for the steel building, the process of recycling and joining metals have becomes inevitable. At the onset, the most commonly-used method of joining steel together was either by bolts or rivets. However, due to the intensiveness of the riveting and bolting process, other methods of joining steel had to be developed, and for this reason, the process of welding steel joints was afterward introduced.
Transformations & Developments of Welding Career
Welded joints, especially, in steel fabrication, are found to be far stronger than riveted or bolted joints, for welded metals are bonded together by means of fusion. In fusion, the base metal or workpieces are heated, melted, and joined together at the molecular level. Moreover, in its earliest form, welding was done by hammering two pieces of red-hot metals together until they fused. This process is now called “forge welding.”
Another early form of welding is the Oxy-fuel welding/cutting. Otherwise known as “oxyacetylene welding” for its use of Oxygen as oxidant and acetylene as fuel, oxy-fuel welding produces high-temperature flame to heat and melt the base metal or workpiece to create a molten pool where filler of similar metal is added to form a molecular bond. Oxy-fuel cutting is somewhat identical to the oxy-fuel welding, but instead of melting the workpiece to create a bond, oxy-fuel cutting uses a different type of torch that produces a flame that could cut through the metal.
The same oxyacetylene welding equipment is employed in brazing and/or soldering, albeit using solder wire instead of filler. Arc welding, on the other hand, uses a similar procedure to oxy-fuel but employs electrical arc rather than flame, and thus it achieves higher welding speed.
Arc welding is the most common metal-welding technology today. Arc welding uses electrical arc (concentrated near the tip of the electrode) to heat and melt the base metals or workpieces that are to be welded along with the filler material that creates a bond at the joints. There are various types of arc welding, and some of the most common arc welding processes are:
Different Types & Processes of Welding
1) Shielded Metal Arc Welding (SMAW)
Shielded Metal Arc Welding (SMAW)—SMAW, also commonly known as “Stick” welding due to its use of rods or stick electrode, is the predominantly used type of arc welding. The consumable electrode serves as the filler material and is coated with flux. The flux coating produces a shielding gas that protects the molten pool from atmospheric effects. The same flux is also deposited on top of the molten pool and forms a material called “slag” to protect the pool as it cools.
2) Flux-Cored Arc Welding (FCAW)
Flux-Cored Arc Welding (FCAW)—FCAW is very similar to SMAW except that FCAW uses a continuous electrode. But instead of being coated with flux material, the consumable FCAW electrode uses a fine metal tube filled with flux.
3) Gas Metal Arc Welding (GMAW)
Gas Metal Arc Welding (GMAW)—Like FCAW, GMAW or more commonly MIG (Metal Inert Gas) welding uses a continuously-fed consumable wire electrode that also acts as filler material to the weld. However, in MIG welding, the wire electrode is without flux and must rely on an external shielding gas.
4) Gas Tungsten Arc Welding (GTAW)
Gas Tungsten Arc Welding (GTAW)—Otherwise known as TIG (Tungsten Inert Gas) welding, the GTAW welding is unlike most arc welding processes that utilize a consumable electrode that also acts as filler material. Contrariwise, TIG welding uses a tungsten electrode to create an electrical arc and uses a separate, manually-introduced filler wire. TIG welding also uses an external shielding gas similar to that of GMAW welding.
5) Submerged Arc Welding (SAW)
Submerged Arc Welding (SAW)—SAW process differs from most arc welding processes for, in the case of SAW, the electrical arc is submerged under a layer of flux. The flux covers the welding from atmospheric contaminants and prevents spatter or sparks from flying. The flux also shields the operator from the intense UV (ultra-violet) light that the arc creates. Moreover, the molten flux serves as an electrical conductor between the consumable, continuous electrode and the workpiece. SAW is usually available in automatic or mechanical form; however, there are portable, manually operated models with pressurized or gravity-fed flux delivery system.
Types & Categories of Welding Jobs
It is basically self-evident that no one can perform perfect welding without having welding skill. Welding skill is the knowledge that can only be acquired through practice. At the onset of the development of the different welding processes, welders generally gained their welding skills through apprenticeship. At present, however, welding courses are already offered to train those who would like to become welders. After learning the basic techniques and principles, the prospective welders must further learn other skills related to welding like the knowledge of how to read technical drawing plans. Moreover, the ideal welders should be proficient in two or more welding types.
Since most modern structures and means of transportation that we use today are made of steel, there is definitely a huge demand for welding skills. Hence, welders will surely never run out of job, and job opportunities for welders are mostly needed in various industries. Here are some in-demand jobs for welders:
1) Pipe Fitter
Pipefitters are generally responsible for pipe layout and installation of all piping systems found in buildings and other constructions, HVAC (heating, ventilation, air conditioning) fabrication and plumbing. Due to their work responsibility, pipe fitters need to acquire additional skills such as the proficiency in reading blueprints and drawing aside from the basic knowledge of laying and joining pipes together.
2) Sheet Metal Worker
The fabrication of items such as those of air conditioning and heating ducts as well as rain gutters require some adroitness on the part of a sheet metal worker. Hence, aside from welding, welders need to have basic knowledge of oxyacetylene welding and soldering process for thin sheets of metal do not need very high-temperature heating process. Sheet metal workers should also be learned in fabricating parts of cars, airplanes, and boats.
3) Fabrication Welder
The fabrication welder is required to cut and weld metals to fabricate parts of machines. Moreover, they are required to follow engineering drawings and specifications. There are two categories of fabrication welders: light and heavy. Light fabrication welders usually work in fabrication companies of car chassis and body as well as in fabrication companies of vehicles, metal chairs or table, water tanks, and reservoir. Fabrication of bridges and shipbuilding falls under the category of heavy fabrication welder. Heavy fabrication welders usually work with heavy and thick metals that need deep welding joints.
4) Welding Inspectors
A certified welding inspector needs to be a very experienced welder as he needs to examine and determine if the welding satisfactorily meets the specified requirements or specifications. To become a welding inspector, one is required to have significant experience in arc welding, gas welding, as well as in pipe welding. Moreover, to be a welding inspector, one needs to be adept at reading blueprints and other fabrication drawings. Furthermore, he has must have necessary skills in drafting. Lastly, the welding inspector is required to have a firm foundation in physics and mathematics.
Welding Jobs / Careers You Can Pursue
Due to the vastness of the scope covered by welding that includes various welding procedures, types, tools and machineries, welding jobs themselves have three general categories, namely, cutters, brazers and solderers, and welders and welding machine operators.
Welding, as a career, is a great choice that doesn’t necessitate a college degree. You can get a welding certificate in as fast as nine months and begin earning a neat wage. Nevertheless, welding can also land you a hefty amount of money if you are good at it. It can even get you employed in some of the most prestigious companies in the world like Space X and NASCAR. Below is a rundown of the different welding jobs you can engage in:
1) Welders and Welding Machine Operators
As mentioned earlier, welders need to know at least two types of welding processes, especially, in the field of arc welding. In manual welding operation, the welder needs to know how to set up the welding machine and must have the knowledge about equipment, materials, and garments that are required for a specific welding job. The same is true of welding machine operators. However, welding machine operators must also be well-versed with various techniques and welding procedures. They should also be adept in using welding machines. It is important to note here that welding machine operation is mostly employed in large-scale production and fabrication using semi-automated welding processes.
2) Cutters
Similar to welding, cutters must have the know-how on using manual and machine cutters that use plasma, oxy-fuel or electric arc to trim or cut a workpiece to its precise dimension and shape. They must also know how to use these tools in cutting and chopping fixed-metal structures such as steel bridges into smaller pieces for recycling or scrapping. On the other hand, cutting-machine operators are employed to dismantle movable large metal structures (ships, airplanes, cars, and locomotives) into their smaller components.
3) Solderers and Brazers
Similar to the welder in various respects, solderers, and brazers don’t use very high temperatures and don’t need to melt the workpieces that are being joined. They instead heat the workpieces together with the solder material to join the workpiece together. Moreover, while solderers and brazers share common work procedures and materials, brazers only engage in melting the soldering material. Lastly, the brazing process requires the workpieces (such as pipes) that will be joined are closely fitted so that the melted soldering material can flow through the gaps between the workpieces via capillary action.
4) Fabrication Welders
Did you ever dream of building a bridge or cruise ships, or even something small as a bicycle or working for NASA or even NASCAR? Welding Fabricators, also referred to as Fabrication welders, do just about this. With the help of engineering drawings, metals are cut into desired shapes and weld together to form a specific structure. Building bicycles or car bodies is a part of light fabrication. Heavy fabrication involves the production of boats, bridge structures, and canes. The demand for fabrication welders is, but not limited, in the areas of construction, aerospace, manufacturing and automotive, etc.
5) Boilermakers
They are welders specializing in fabricating, installing, maintaining, and repairing of large tanks, which hold liquids and gas. Constructing these vats out of metal always withstand extreme pressure – hot water boilers; storage tanks and steam generators are some examples of this. They are known for making the custom steel plates and pipes, which make up these big containers. Boiler making training most of the times is involved in welding programs.
6) Pipeline Welders and Pipefitters
A lot of gas, water and oil industries rely on pipelines for the transport of their product throughout the world. The ounce of constructing and repairing the pipelines fall on pipeline welders. The professionals who install the piping system are known as pipefitters. With the help of specialized welding skills, they lay and bond pipes together. Pipefitters and pipeline welders need to be able to read blueprints. There is a need for these types of skills for jobs in plumbing, construction, HVAC, manufacturing, oil, gas, water, and other utility industries.
7) Structural Iron and Steel Workers
At times, structural steel welders, also known as “Ironworkers, are the people who work to assemble the steel structure of large buildings. Ironworkers, at times, work at very high altitudes. Their job is full of dangers, and it is not uncommon to see an ironworker missing a part of a finger or the whole thing. The unpredictable speeds and directions of the wind can easily blow a hanging beam in any direction causing severe injuries to the ironworkers.
Even facing these dangers, welders and Ironworkers can work side-by-side. The Ironworkers can be working on making structural connections, while the welders weld on the brackets or tabs.
8) Underwater Welders
The area of underwater welding is a unique career path. Unlike structural welders, who often work at heights, underwater welders work in the rigging, deep-sea fitting, cutting, inspecting, welding, and repairing heavy metal products such as Naval ships, submarines, oil rigs, gas pipelines, etc. due to intensity of the work, it’s crucial to have a physical exam for underwater welders. Not only this, but they should also be certified divers.
9) Production Welding Jobs
One can find these jobs in a factory or assembly-line type of production facility. In production type of setting is where you will find most MIG welding jobs. This is in large part due to its cleanliness and speed. From working on a large pressure vessel to directly welding brackets onto a sheet metal or a beam, there is a lot of work for production welder.
Their minimum wage starts mostly from $30 an hour. Factors that determine their rate depend upon the setting and the company that they are working for. Some of the higher paying production welding jobs are in heavy equipment companies like John Deere, Case, Caterpillar, and Volvo.
10) Industrial Maintenance Welding
You will find maintenance welders in factories, extensive manufacturing facilities, and oil refineries. Their tasks include piping, installation of new machinery, repair welding, and ductwork. Other skills, such as basic electrical and pneumatic knowledge are often needed.
11) Ship Building
In the USA, most shipbuilding companies can be found on the Gulf Coast, in either Florida, Alabama, Louisiana or Mississippi. Many larger shipbuilding companies offer apprenticeships where one can start with no to little experience as a welder. After completing the training, one gets certified as a welder and can earn a minimum wage of 20$ per hour. If you already have the experience, then you can start as s full-fledged shipbuilder.
It is easy to get a job in this field. The ease of finding employment is because of the magnitude of the work that ship companies work on and the length of time that it takes to complete a project.
12) Construction Welders
Welding is an essential aspect of construction, and as such, it is indispensable in the construction industry. You will find welders engaged in some aspects of residential construction and commercial construction because metal is a crucial material in most constructions. Construction welders are usually exposed to a high level of risks because they need to work outdoors. Sometimes, they work on elevated grounds—several meters up high.
In many industrialized countries, construction welders receive hefty wages, while welders get only the minimum wages in developing countries.
The job descriptions of welders in residential constructions differ much from those engaged in commercial constructions. Welders employed in residential constructions are often skilled in smaller welding tasks, like welding pipes and other smaller welding tasks.
Welders in commercial constructions, however, undergo a higher level of training to accomplish challenging welding jobs. They are engaged in locations that require a significant amount of metal components. They may work in the construction of high-rise buildings and lofty bridges. Hence, their training is more specified and rigid.
13) Tack Welder
Another type of welding job involves tack welding. It involves tiny welds done to hold items in their places. Tack weld aims to keep the items in the correct positions to enable the performance of the main weld. It allows you to avoid holding heavy metal pieces together while you weld. Instead, you only engage in tack welds to provide strength and stability to the items to enable you to engage in the main weld.
Thus, if you work as a tack welder, you only position the pieces properly by performing small and light welds. The lead welder does the welding of the mainframe. In this way, the job becomes easy, smooth, and compartmentalized.
14) Industrial Shutdown Welders
The equipment and components utilized in many industries experience wear and tear because they are susceptible and exposed to tension and friction. As such, they should be maintained regularly. However, there are instances when the equipment must be shut down totally for immediate and more comprehensive repairs and maintenance. This type of shutdown is referred to as “shutdown maintenance.”
Welders—who engage in shutdown maintenance—are also referred to as shutdown welders (industrial). Companies usually hire these welders. Companies never outsource them. These welders work as a regular contingent of the company, and they work inside the plant.
The company mobilizes the industrial shutdown welders once there is a need for a temporary shutdown of the plant for maintenance. This maintenance may take several months or weeks.
15) Rig Welders
One of the biggest and most profitable industries in the world is oil and gas rigging. This industry also requires welders as an indispensable aspect of their workforce, whether it involves offshore or on-land rig sites. Rig welders have the task of welding the artificial steel scaffolds in offshore rigs. They are also engaged in constructing the whole on-land rig station.
They are not only engaged in rig construction, but they are also tasked to do the maintenance and repairs of the rig. Moreover, these welders relocate to the sites for immediate deployment, especially in case of emergency. They also weld pipes and collars and engage in all types of welding jobs.
The welders who engage in rig welding are handpicked for their exceptional training and strength because they are required to labor in very tough conditions. Moreover, they are also expected to perform well even during dangerous situations to avoid the onset of catastrophe. Nevertheless, since their jobs come with more risks, they often get hefty wages.
16) Military Welders
Military welders are those welders who work in military camps and other military installations. They are enlisted in the army and form an indispensable contingent of the different military divisions. Because of this, they need to undergo basic military training. They also get oriented about the military protocols. Hence, they should be in good physical condition.
The tasks of military welders include repair, manufacturing, and maintenance of everything used in the military. Besides, they are often situated in danger zones, including war zones. They weld damaged vehicles and even aircraft carriers.
Military welders are also required to stay in the military ships and vessels for extended periods to look after the maintenance of military ships.
17) Aerospace Welder
If you think you are a top-notch welder who can qualify as an aerospace welder, then go for it. As an aerospace welder, you will get to work on rocket ships and may have a very fulfilling welding career afterward. You also get to work on technology that involves rocket science. You can apply, for example, to Space X or NASA.
The competition for an aerospace welder is stiff considering that it is high-paying and necessitates a high level of welding skills. Yet, if you get hired, you will indeed find this job rewarding.
18) Welding Inspector
Welding inspectors are experienced welders who got a deeper understanding of the welding process. They are not much engaged in welding jobs, but they inspect the welds done by others. Their jobs include ensuring that the welding standards on quality and safety are followed to the letters.
19) Welding Engineer
Welding engineers have highly specialized jobs in designing and planning segments of industrial projects. They do not perform welding. Nevertheless, they are the ones who develop the necessary procedures that welders should follow in a particular project.
They are the ones who determine the materials to be welded and how they should be welded. Moreover, they got the responsibility for ensuring that the welds will be safe and strong when done.
20) NASCAR/Automotive Racing
You may think that welders are not needed in motorsport or any automotive racing. Yet, they are required there. The reason for this is that motorsports require much welding since automobiles are wrought in metal. These welders involved in motorsports ensure that there is no weld failure in such an environment.
Welders in this field should have meticulous attention to details. They should have a high level of welding skills to qualify for such a job. They also get to work for companies like NASCAR.
Conclusion
You can engage in welding as a hobbyist or as a professional. As a professional welder, it will indeed help if you enhance and hone your welding skills to go up higher in the welding career ladder. The welding career for welders is a far-reaching career that could lead you to work in prestigious companies. In fact, it can land you in industries involved in rocket science which can provide you a hefty amount of salary.
Remember that your only limitations as a welder are set only by your ambitions and desire. And if you excel in your craft as a welder, you will surely open myriads of opportunities for you. Moreover, you can find a lucrative job that can help you stay afloat financially for the rest of your life.