June 11, 2021
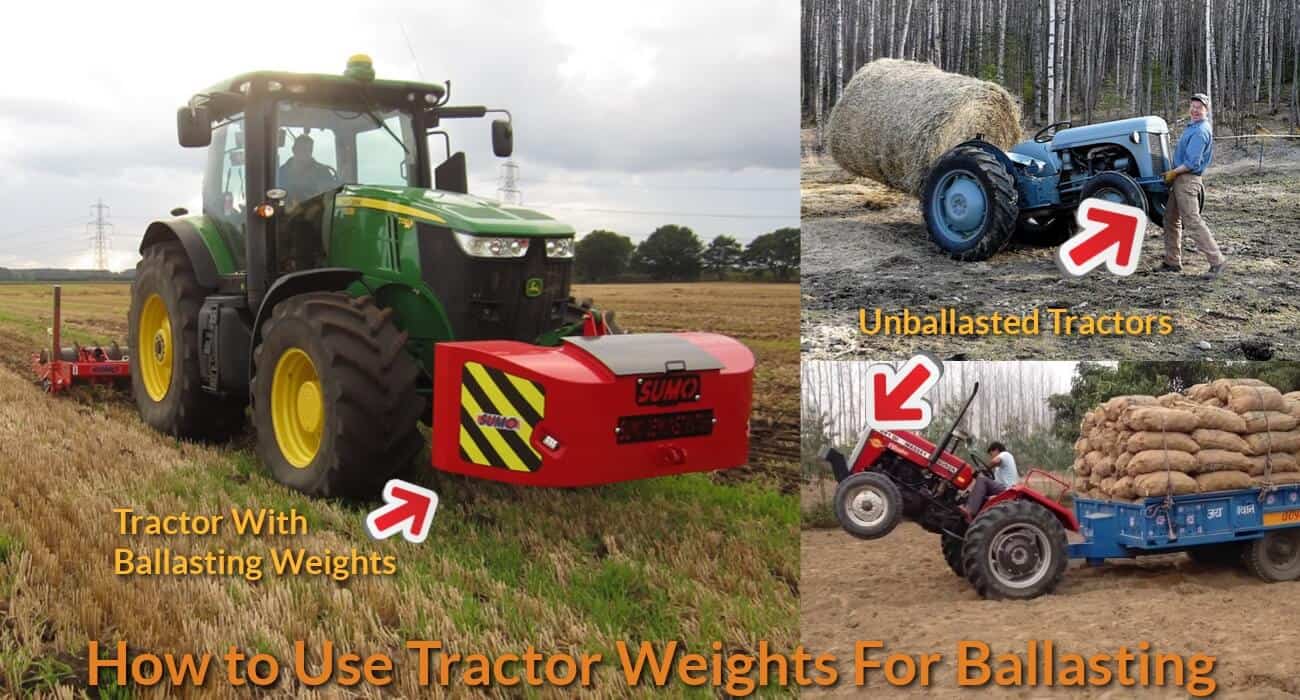
In order to effectively use a tractor to accomplish any farm activity or task, the tractor needs the right implement and attachment. However, this is not only the case or requirement for there is also the subtle thing called “ballast.” In many compact and midsize tractors, we would often see that the front loader and backhoe implements hang on both ends of the tractor. With this design, you can never employ both implements at the same time. Admittedly, there is a reason for this arrangement, and that reason is for counterweight or ballast. When the loader is employed, for example, the backhoe acts as a counterweight and when the backhoe is employed, the loader bucket functions as ballast or anchor.
Should You Use Ballasting Weights On Your Tractor?
Ballast or added weight can either have a beneficial or adverse effect on the tractor’s overall performance. Ballast or counterweight can provide stability to the tractor and its implement. In the same manner, the tractor gains better traction due to this added weight. However, added weight can cause the engine to work harder and burn more fuel, and can eventually bog down when passing over soft ground.
Every tractor of any made has its “base weight.” This base weight is the designed weight of a tractor without any attachment or implement. It is only plausible to increase the tractor’s weight through attachments, implements, and ballast, but it is impossible to decrease the base weight without removing any of the tractor parts.
The main essence of ballast is to acquire and transfer as much engine horsepower to the ground. Without the ballast, much engine horsepower is lost employing wheel slippage, especially, when towing implements. Lost horsepower translates to wasted fuel and greater wear on the wheels; thus, eventually adding to the cost of operation. As a general rule, the ballast is added to ensure that at least 10 percent of wheel slip is attained. New models of tractors have performance monitor that readily identifies the wheel slip. Over-ballasting, on the other hand, can lead to overstraining of the drivetrain and excessive fuel consumption.
Types of Ballasts
There are different types of counterweights or ballasts. Some are subtly shaped that they are almost unrecognizable from a certain distance. The ballast or counterweight needs not to be expensive. Some ballasts are homemade like concrete blocks or cylinders. The tractor implements, for example, can certainly act as a ballast. Here are some of the popular ballast types are:
1) Ballast Boxes
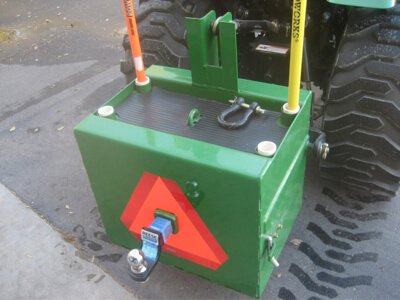
Ballast boxes are counterweights that are mainly attached to the rear of the tractor by way of a three-point hitch to balance the front loader implement. In many cases, the ballast boxes are simple steel boxes that can hold a measured amount of weights in the form of gravel or sand. Some ballast boxes are half-filled with concrete or steel ballast, with room for additional counterweights such as concrete blocks or cylinders to obtain a more specific amount of ballast. Other ballast boxes are made from a single reinforced concrete block with attachments for three-point hitch or 3PH. Aside from purpose-built counterweights, the homemade ballast box is becoming popular, especially, to DIYers who would instead build than buy.
2) Suitcase Weights
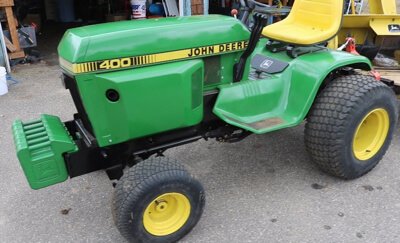
Suitcase weights are compact and small counterweights that can be grouped and held by a bracket or added to an implement to obtain a desired amount of ballast. This ballast type can also be fastened to an implement attached to a tractor. Suitcase ballast is commonly found in front of tractors without the forward implement.
3) Implement Ballast
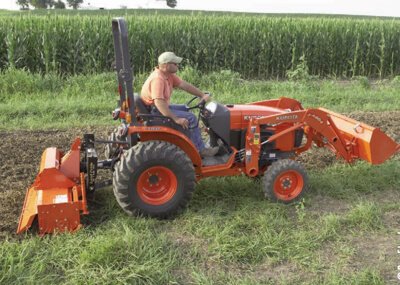
Implements are heavy pieces of machinery that can act as a counterweight to another implement. As mentioned above, some tractor manufacturers and distributors usually hang two sets of implements to a tractor and use one implement while the other acts as ballast. If the implementation does not have the necessary weight, suitcase ballast is added to the implement. The commonly used implements—that act as ballast that can accommodate suitcase weights—are rotary cutters, farm tillers, landplane or box blade.
4) Tractor Wheel Weights
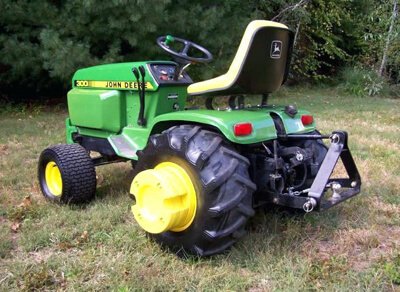
Ballasting the wheels provide more direct approach on placing the load to the axle. There are two methods used in wheel ballasting, namely: liquid ballast and wheel weights. Liquid ballast is achieved by adding fluid inside the tire. There are several types of fluids that can be utilized for this method. Some of these liquid ballasts are water, methanol, glycol, and calcium chloride. However, liquid ballast tends to increase tire stiffness that can lead to bigger problems. Moreover, the liquid ballast is much difficult to install and adjust.
On the other hand, the use of wheel weights is the more straightforward means of ballasting the wheels for this method only requires you to fixate the ballasts on the wheels’ metal rims. Wheel weights are mostly made from solid cast iron, plastic encased concrete, or sand ballast. These wheel weights are categorically considered as suitcase ballast; however, wheel ballast is considerably more effective than 3PH suitcase ballast as the actual weight is directly applied to the axle. Wheel weights should be installed or removed in pairs to maintain the balance of the ballast from side to side.
While the wheel weights are centered around the axle, other ballast types are mounted either ahead or behind the axle. These placements of ballast create a leverage effect called “weight transfer.” This leverage effect allows you to add greater weight to the axle than the actual weight of the ballast.
How to Calculate & Determine the Ballast?
To determine the ballast required for a given tractor, you will need to figure out the tractor’s parameters and other specifications that are found in the operator’s manual (OM) of the tractor. These parameters or specifications include the weight split table, the tractor’s horsepower rating, and the tractor’s maximum ballast limit.
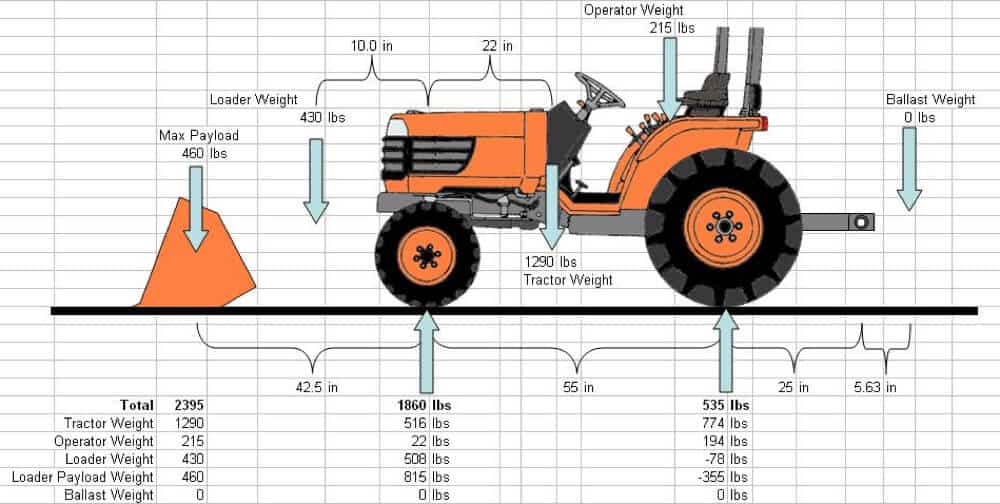
The weight split is the percentage of weight that is required to be carried by the front and rear axles. A four-wheel-drive tractor, for example, has a range of 51-55% for the front axle and 45-49% for the rear axle. You should aim for the middle value of these percentage, (i.e., 53% and 47%, respectively.) Weight split for two-wheel rear drive tractors has 25-35% for the front axle and 65-75% for the rear axle. Along with horsepower rating and tractor’s maximum ballast limit, the weight split is vital in determining the following weights:
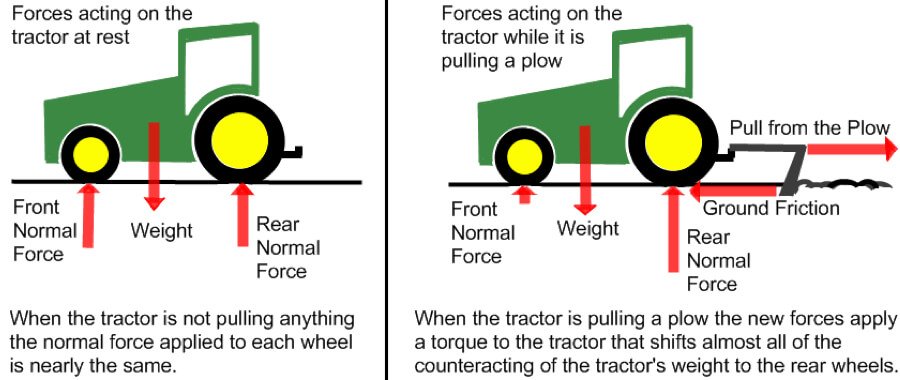
1) The Desired Total Tractor Weight
This is achieved by multiplying the weight/power ratio by the tractor weight. The weight/power ratio is stated as lbs/hp. As in weight split, you should aim for the middle value. In some tractors, there is a so-called ballast limit. The desired tractor weight should not exceed this ballast limit; but if ever it happened, the ballast limit is used instead of the desired total tractor weight.
2) Desired Axle Weights
To calculate for the desired front axle weight, the front axle weight split percentage is multiplied by the desired total tractor weight. To calculate for the desired rear axle weight, simply subtract the desired front axle weight from the desired total tractor weight. However, the desired axle weight should not exceed the load carrying capacity of each tire.
3) Amount of Ballast
To determine the amount of ballast required for each axle, subtract the unballasted axle weight from the desired axle weight. The unballasted axle weight can also be found in the operator’s manual.
Additional Advice & Warnings
Tire Pressure
Before heading out for any farm activity, it is essential to check the tire pressure. After installing the necessary implement and its corresponding ballast, it is necessary to adjust the tire pressure. Many tractor users never bother to adjust the tire pressure in accordance to the axle load or as per OM’s instruction. This can cause a detrimental effect called “engine hopping.” Moreover, the overly inflated tire can cause tire slip and unnecessary over-compaction of the ground.
To inflate the tractor’s tire with the optimum pressure, you need to consider the tractor’s weight, the added ballast and the weight of the implement that is pulled or carried. After calculating the first two factors, you can figure out the implements weight using the user’s manual. However, due to the leverage effect, the implement’s weight is more to the nearest axle than the implement’s actual weight. Then after, you can figure out the recommended tire pressure from the tractor’s OM or from the tire manufacturer’s website. Never forget to adjust the tire pressure every time the implement is replaced, or every time there is a sudden change in temperature.
Lastly, the non-adherence to the manufacturer’s recommended setting can be ground for voiding the tire warranty.
Best Tractor Ballasts & Weights In The Market
Conclusion
To get the optimum performance from your tractor, it is best to follow the recommended ballast and tire pressure adjustments found in the operator’s manual. It is also essential to learn how to calculate the desired axle weight and tire pressure to minimize the effect of wheel slip and prevent the impact of engine hop that could eventually lead to a costly operation.