June 11, 2021
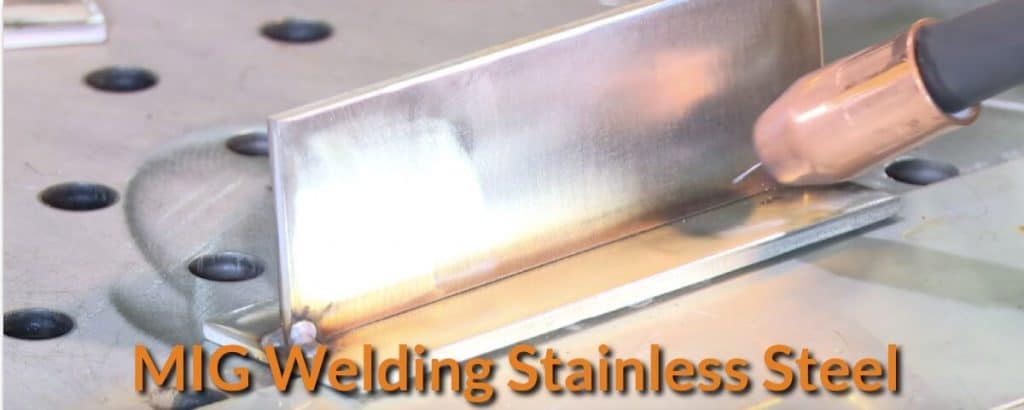
MIG or Metal Inert Gas welding otherwise known as Gas Metal Arc Welding (GMAW) is one of the most popular and widely used arc welding processes for joining stainless steel and other metals. In MIG welding, the continuous wire electrode is automatically fed to the welding torch at a user-defined speed. Likewise, the externally-fed shielding gas is also fed to the torch at prescribed pressure settings.
Major Factors To Consider:
Hence, before starting any MIG welding task, it is important to take into consideration the following factors:
- Type of metal to be welded.
- The metal’s thickness.
- Preparation and cleaning of the workpiece.
- Type of metal-transfer mode required.
- Setup of the MIG welding machine.
Procedures For Using MIG To Weld Stainless Steel
Most MIG welding procedures use constant voltage power outputs for energizing the electrode and creating the electric arc. In constant voltage output, the voltage remains constant while the electric arc current and the resultant heat fluctuate. Moreover, the changes in arc lengths (as influenced by the voltage) have an inverse effect on the current and resultant heat. Therefore, a short arc, for example, produces much higher current and heat.
MIG welding generally uses direct current, electrode positive (DCEP) power supply, although DCEN or negatively-charged electrode and alternating current (AC) power supply are also used and available but unpopular.
MIG Welding Stainless Steel Basics
Despite the fact it doesn’t necessitate great skill to perform MIG welding, it, however, requires some understanding of basic welding skills to perform MIG welding. The most important settings in MIG welding include voltage setting, the speed of wire (electrode) feed, and the type of shielding gas and its flow rate.
It is highly recommended for beginners in MIG welding to first hone their basic stainless steel MIG welding skills on less expensive materials such as carbon steel, for the techniques used in welding stainless steel/nickel-based alloys and carbon steel are very similar. Moreover, although most welders believe that MIG welding is the easiest to learn, it is however very difficult to master.
MIG Settings For Stainless Steel Welding
To facilitate the MIG welding setup, MIG welding manufacturers have included a helpful table that is usually affixed to the MIG welding machine. This table enumerates the power supply, wire types and shielding gases, diameter size of electrodes, shielding gases, suggested voltage, and wire feed rates. To determine the voltage and wire feed rates, one should first establish the thickness as well as the (electrode) wire diameter. Afterward, one should locate the intersection of the said data on the table. The values of the numbers on the intersecting columns correspond to the voltage/feed rate settings. These values may differ from one manufacturer to another manufacturer. Furthermore, the shielding gas flow rate is sometimes found within the machine’s manual.
For welding stainless steel, Millermatic’s suggestions include stainless steel wire for DCEP power supply, Tri-Mix (905 He/7.5% Ar/2.5% CO2) helium-argon-carbon dioxide mix as shielding gas at 20-30 cubic feet per hour. The common intersection of the column for wire sizes and workpiece gauge or thickness presents the suggested voltage/feed rate settings.
For example, to weld a 1.9mm stainless steel using 6mm diameter wire, the voltage setting should be 4 volts with the feed rate of 65 feet per minute. However, if problems—like wire burn-off before reaching the workpiece—occurs, the wire feed rate can be slowly increased until a cracking sound is eventually produced. At this point, the rate should be gradually decreased. If the wire continues with a cracking sound, you should either step-up the voltage one step higher or decrease the rate further.
Mode of Metal Transfer
The metal transfer is the process of how the molten filler material from the wire is transferred from the electrode to the workpiece. MIG welding uses three modes of metal transfers, namely:
1) Spray Transfer
Spray transfer which occurs with a rapid transfer of electrode metal through stable voltage electric arc to the workpiece resulting into a clean and high-quality weld line. A variant of this metal transfer called the Pulsed-Spray transfer occurs when the electrode metal melts due to the pulsing current which eventually creates molten droplets that fall on the workpiece on every pulse.
2) Spray Transfer
Spray transfer which occurs with a rapid transfer of electrode metal through stable voltage electric arc to the workpiece resulting into a clean and high-quality weld line. A variant of this metal transfer called the Pulsed-Spray transfer occurs when the electrode metal melts due to the pulsing current which eventually creates molten droplets that fall on the workpiece on every pulse.
3) Short-circuit Transfer
Short-circuit transfer which happens when the molten filler spans the gap between the electrode and the workpiece and short-circuits and momentarily extinguishes the arc. This occurrence is due to the slow feed rate.
4) Globular Metal Transfer
The globular metal transfer which occurs when a largely molten globule builds up at the end of the electrode and falls to the work piece either by gravity or short circuit, creating a blob of filler material.
5) Mode of Transfer
The mode of metal transfer depends on two factors—voltage and shielding gas. For example, short circuit transfer is achieved by using lower voltage output along with CO2 gas shielding. Globular and spray transfer are attainable via the use of high voltage output along with argon gas shielding.
Choosing the Right Gases and Electrodes for MIG Welding Stainless Steel
As mentioned above, MIG welding machine manufacturers have included a table of materials and parameters for their products to provide MIG welders with basic knowledge on how to go about with the use of MIG welding equipment. Moreover, this table indicates the choice of shielding gas to be used in MIG welding, and it would be good to note that the most common electrode/gas combination used for welding stainless steel is the E308L electrode with C2 gas.
The typical shielding gases used in stainless steel MIG welding include the following:
- Tri-Mix Gas (90% Helium, 7.5% Argon, and 2.5% Carbon dioxide).
- C2 (2% Carbon Dioxide or CO2 and 98% Argon).
- C5 (5% CO2 and 95% Argon).
- C10 (10% CO2 and 90% Argon).
- C25 (25% CO2 and 75% Argon).
Welding Rods For Stainless Steel
When searching or buying anything, it is valuable to know the proper name or nomenclature of an item being searched or bought. For example, Gas Metal Arc Welding or GMAW is the proper name for MIG welding. Similarly, GMAW electrode is the more appropriate name for MIG wire. Some of the commonest GMAW electrodes available today are ER 308L, ER 309L, and ER 316.
Potential Issues & Problems
When MIG welding stainless steel, it is advisable that you first hone your skill on less expensive metals like carbon steel before you attempt to tackle stainless steel. This is due to two apparent issues— weld joint distortion and MIG gun cord/liner—which can ruin a welding project. On the one hand, stainless steel readily distorts once heat is applied to it. The most effective means to arrest the metal’s undesirable distortion is to brace the workpiece together and tack weld the pieces, thereby distributing the heat before applying full weld.
On the other hand, MIG gun cord/liner issue occurs due to the friction on the stainless steel electrode that prevents a smooth passage through the gun cord/liner. When the flow of the electrode wire slows down, the arc will melt the wire up to the MIG gun or torch’s tip, and this results into the fused tip. This issue can easily be rectified by keeping the cord straight.