June 11, 2021
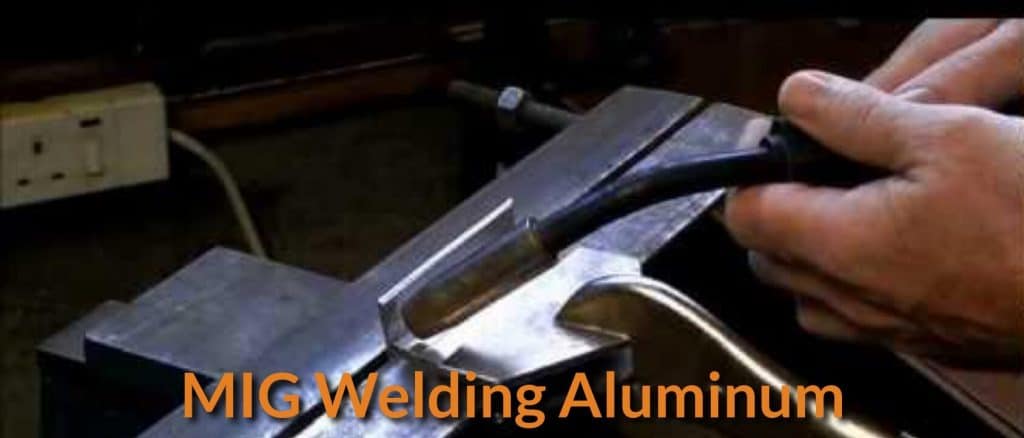
There is usually a misconception that MIG welding aluminum is similar to MIG welding mild steel. Contrariwise, these two welding processes are quite different from each other, and it would surely be a mistake if one would apply the same knowledge and welding methods on both types of welding jobs.
Factors to Consider When MIG Welding Aluminum
There are several factors that you must consider when MIG welding aluminum and some of these factors include the following:
- First, you must consider the thickness of material appropriate for MIG welding on aluminum. The appropriate material thickness for MIG welding on aluminum is 14 Ga. or more. The weight or heaviness of material usually relies on the equipment’s output capacity. Hence, if you are welding aluminum which is less than 14 Ga or .074 inch, it is advisable for you to use AC TIG or pulsed MIG.
- Second, you must consider that aluminum is softer than steel. Since MIG welding utilizes consumable wire electrode together with a shielding gas that is fed continuously via a welding gun, you should at least recalibrate your welding style to adjust to the softness of aluminum. Moreover, your feed wire should be larger than the one you would usually use when MIG welding steel.
- Lastly, you should bear in mind that aluminum is a much better heat conductor, and as such, you need to regulate better your power supply and the electrode’s feed rate.
Preparation For MIG Welding Aluminum
1) Consider the Thickness
A professional welder would definitely know when to use MIG welding for aluminum and when to opt for another type of welding equipment. Since aluminum absorbs more heat than steel, you should know which thickness of aluminum is appropriate for MIG welding. The minimum thickness of aluminum should be from 14 Ga to 18 Ga. If you are going to work with aluminum that is thinner than the abovementioned range, you should instead opt for the TIG welding.
The main reason why you should only attempt to use MIG welding for thinner pieces of aluminum is that, when welding thinner aluminum pieces, the weld puddle readily falls through the workpiece if you are not quick enough. Additionally, when using wire welder, you would readily notice unexpected burning through. Unlike in MIG welding mild steel wherein you must be slow when moving the MIG gun to produce deep penetration, with aluminum MIG welding aluminum, the weld puddle readily falls through like a “soaked foil.”
If you are not careful or experienced enough when engaging in aluminum MIG welding, you may end up ruining your workpiece. Moreover, it usually takes several practice sessions before you can perfect MIG welding on aluminum.
The advisable equipment to use when handling aluminum is that of the 115-volt welder. This equipment can handle up to 3 mm or one eight of an inch-thick aluminum. It can likewise provide adequate heating for the welding process. However, you can also use a 230-volt equipment which is capable of welding up to 6 mm or one-quarter inch thick of aluminum. It is also advisable to use a 200 amps equipment if you intend to regularly weld aluminum.
2) The Shielding Gas to Be Used
Another factor that must be considered when MIG welding for aluminum is the shielding gas. The aluminum MIG welding requires pure argon, while steel MIG welding requires C25 gas which consists of 25% CO2 and 75% argon. The spray transfer process generally occurs in MIG welding because of the help of pure argon shielding gas. However, if you are working on thicker aluminum with more than half an inch thickness, you can combine 25 up to 75 percent of helium to pure argon, and this combination would readily permit deeper and greater penetration onto the workpiece.
3) The Type of Electrodes to Be Used
The choosing of aluminum electrodes plays a crucial role in the success of MIG welding on aluminum. The thickness of electrode likewise is important. Moreover, you would surely find it hard to weld if you would use thinner wire because the thinner wire is not easy to feed. On the other hand, thicker wire will require more current to melt. Hence, it is necessary to settle for the middle ground and use less than 1 mm in diameter of welding aluminum or .035. Your best choice would be 4043 aluminum. You can also use 5356 aluminum which is obviously easier to feed but may necessitate more current.
4) Polarity Setting
When engaging in aluminum MIG welding, you should set your machine to Direct Current Electrode Positive polarity or DCEP. This polarity setting is also known as the reverse polarity wherein the electrons in the circuit move from the machine down to the ground cable and back again via the gun. This setting is critical for effective and efficient welds.
Welding Techniques for Aluminum MIG Welding
Double the Welding Speed
It is surely advisable when MIG welding on aluminum to use similar voltage settings to the voltage settings that you would use when MIG welding steel. However, instead of using the same speed, you should double up your travel speed. At first, you may find it inconvenient to double up your speed, but you would eventually get used to it. You must use spray transfer when welding with aluminum, and this spray transfer method is different from MIG welding on steel. With spray transfer welding, minute aluminum particles are sprayed onto the weld puddle. Furthermore, this process requires adjustments on the welder’s part and additional voltage boost, together with a proper gas mixture.
Master the Push and Pull Methods
MIG welding aluminum requires you to utilize forward welding direction using your forehand to provide push motion. This allows you to ensure that the shielding gas sufficiently shields the weld puddle. If the weld puddle is not completely covered with shielding gas, chances are, you would produce dirty welds. This happens if you use pull effort on the weld puddle in aluminum welding.
Right Angle for MIG Welding Aluminum
It is also necessary that you sport a good angle when MIG welding aluminum. The ideal angle ranges from 10 to 15 degrees torch angle. While welding, you should also sport a pushing posture on your torch instead of the pulling position. You should also engage in a steady and straight torch movement to keep the impurities from the weld puddle. Likewise, to produce neater and consistent welds, it is advisable to push forward and pause before pushing forward again.
The Need for Removing Oxide
A lot of newbie welders often ask why it is first necessary to rid the aluminum of oxide before welding, and the answer to this query is succinctly simple. First, oxide melts slower than aluminum, and if you leave oxide on the aluminum that is to be welded, you would have a hard time fusing together the aluminum pieces. Hence, it is necessary to clean the workpiece first, before engaging in welding. You can do the cleaning by simply using a brush wire for aluminum. It should be aluminum brush wire because there is a risk of contaminating the workpiece if you are going to use other types of wire brush.
Length of Wire Stick-out
There is a need for longer wire stick-out when engaging in aluminum MIG welding. In aluminum welding, the spray transfer method is utilized; moreover, the aluminum heats up fast. For this reason, you need to utilize longer wire stick-out of around three-quarters of an inch to an inch length. On the contrary, in MIG welding with mild steel, you would need shorter wire stick-out of around one-quarter of an inch.
Using The MIG Spool Gun (Optional)
The speed of travel during aluminum welding is faster. But, it is an option you can consider if you efficient welding job done. It only takes 45 seconds to travel 12 inches, which is equivalent to the ability of travel 0.266 inches per second or 16 ipm (inches per minute) travel speed of welding aluminum.
Pros and Cons of Using MIG Welding
- MIG welding is ideal for doing a lot of welding works, especially, with non-ferrous materials. Yet, MIG welding, as a welding option, also has its own disadvantages and advantages. On the one hand, it can weld a wide range of alloys and metals, and for this reason, it affords welders a lot of versatility when welding. It can also be very convenient to use, for it can be used in all four positions. It likewise produces less weld spatter and leaves no slag. Moreover, it allows for better speed, quality, and control because it continuously feeds wire, and thus freeing both hands of the welder during the welding process.
- On the other hand, it is also fraught with disadvantages, because it is not ideal for use with very thick metals. It is likewise less portable than that of the arc welding, considering that MIG welding necessitates the use of inert gas; moreover, it requires a faster cooling process. Lastly, compared to TIG welding, it creates less controlled and sloppier weld.