June 11, 2021
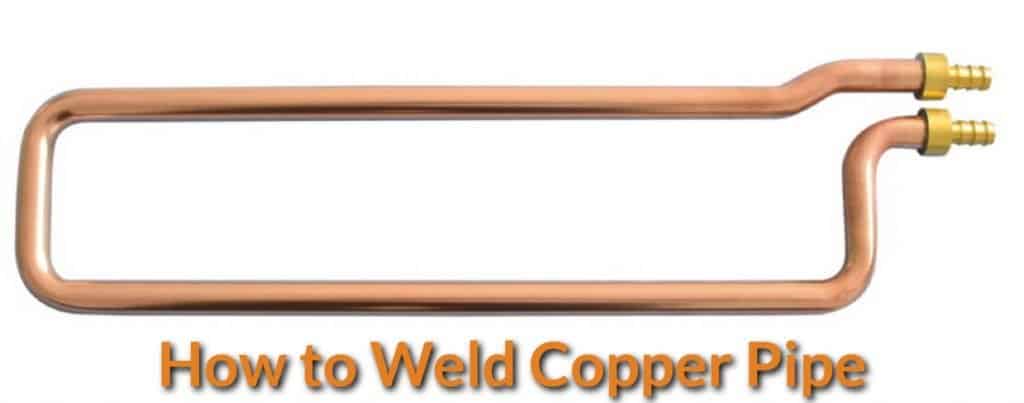
Copper welding is more complicated as compared to metal welding. As a result, most people prefer to weld copper pipe using the soldering welding technique. However, we are going to show you how to weld copper pipe using the GTAW & GMAW welders.
Copper is a naturally occurring, directly-usable metallic form or native metal that does not need to be extracted from its ore. As an ancient metal, human’s use of copper as tools, weapons, or adornment even predated the invention of the earliest forms of writing. Copper’s malleability, ductility, and high conductivity to heat and electricity make the metal a very popular building and industrial material up to the contemporary time. Copper is very workable and can be fashioned into many different end-products such as electrical wires and cables as well as tubes and pipes.
Why Is Welding Copper Pipe More Difficult As Compared To Soldering?
Welding copper pipes can be tricky, if not difficult, due to the metal’s excellent conductivity to heat. This high thermal conductivity is the reason why many craftsmen prefer soldering or brazing copper pipes rather than welding it. This is because bonding copper pipes using brazing or soldering is less complicated and more controllable than welding copper pipes. Moreover, bonding copper pipes using solder is cheaper than arc welding. However, the resulting bond from soldering or brazing is not as strong as that of a welded copper. The reason for this is that with welded copper, the copper pieces are joined together via fusion.
Types of Arc Welding Process
Although there are around five types of arc welding processes that are presently utilized, there are two welding methods that can be best used to weld copper. These are the Gas Tungsten Arc Welding (GTAW) and the Gas Metal Arc Welding (GMAW).
1) Gas Tungsten Arc Welding (GTAW)
Like most arc welding processes, GTAW or more commonly known as Tungsten Inert Gas (TIG) welding uses electric arc to heat and melt both the workpiece and the filler. A shielding gas like helium or argon is introduced at the tip of the torch to protect the molten weld pool from atmospheric effects as it cools and solidifies.
Unlike most arc welding methods like those of shielded metal [SMAW], gas metal [GMAW], and flux-cored [FCAW]) that use consumable electrodes to pass the electric arc to the work piece. TIG welding uses a non-consumable electrode in the welding process and can be used to create a weld joint between the workpieces with or without a filler material. The filler material in GMAW, SMAW or FCAW processes likewise acts as the electrode that carries the electric arc to the workpiece, while in TIG welding, a separate filler wire is used. Furthermore, a filler material may or may not be introduced during the TIG welding process.
2) Gas Metal Arc Welding (GMAW)
Otherwise known as Metal Inert Gas (MIG) welding, GMAW works similarly as the shielded metal (SMAW) that uses its electrode as filler material. However, the SMAW system uses a series of short rods as its consumable electrode during the welding operation, while in MIG welding, a continuous “wire” electrode is fed automatically to the welding torch at a user-defined speed. Likewise, the shielding gas is fed at a regulated setting.
Power Supply
While TIG and MIG welding procedures are generally the same, there are some distinct differences between the two, especially, in the equipment used. TIG welding uses a constant current power supply to produce an electrical arc. With this type of power supply, the heat remains constant, while the electric arc distance and voltage change. Negatively-charged direct current (DCEN) is the preferred polarity used in TIG. However, DCEP (positively-charged) can also be used but is not so popularly utilized.
On the other hand, MIG welding generally operates on a constant voltage power source wherein the voltage (in volts) remains constant while the current, along with the electric arc and heat, fluctuates. MIG welding usually operates on DCEP but can also be operated with DCEN or alternating current.
Other Differences
As mentioned above, the electrode used in TIG welding is non-consumable, while MIG welding uses an automatically fed, consumable electrode wire that also acts as a filler. The filler wire in TIG welding is manually introduced into the weld puddle.
Preparation of Materials
Before commencing with any welding job, it is important to source out and select the best materials available. For example, the copper pipe workpiece as well as the filler rods or wires should be clean and free from dirt, oil, grease, paint or any other impurities. The surfaces where the weld joint will occur should be thoroughly cleaned with the steel brush or wet/dry sandpaper. Moreover, metal-plating like nickel or chrome-plated copper pipes should be avoided to reduce the risk of producing toxic fumes during the welding process.
Types of Available Copper
For copper materials, there are three grades of copper that are currently available in the market. These are the following:
- Oxygen-free Copper—This material has the highest electrical conductivity and is the most readily weldable. However, porosity can be an issue if proper filler material like non-deoxidized filler metal is not used. Oxygen-free copper contains no more than 0.02% oxygen.
- Phosphorous (P)-Deoxidized Copper—The use of P-deoxidized copper prevents any risk of porosity in the welded product. It may contain about 0.05% of both phosphorus and arsenic.
- Tough Pitch Copper—This material is the least desirable grade of copper as it inherently contains the largest amount of oxygen (at less than 0.1%) in the form of copper oxide (CuO).
Types of Filler Wires
For best copper welding results, whether using TIG or MiG welding, it is essential to use filler metals with Manganese (Mn) and/or Silicon (Si) content as deoxidants. The most often preferred fillers are ErCu and ErCuSi-A. ErCu filler contains 0.45 of Mn and Si with 0.8% Tin (Sn) to facilitate fluidity. ErCuSi-A is the preferred filler metals for welding P-oxidized copper as well as tough pitch copper containing 1% Mn and 3% Si as deoxidants.
Shielding Gas
Another essential item in welding copper is the use of appropriate shielding gas while doing the weld. Typically, Argon (Ar), Helium (He) or the combination of both gases (like Argon/75 Helium mix) is suitable for welding copper depending on the work piece’s thickness; however, 100% Helium gas is currently gaining popularity.
Step-by-step Copper Welding Procedures
1) Preheating
Due to the copper’s high thermal conductivity, it is important to preheat the metal (if it is more than 2mm or 0.01 inch in thickness) before any welding can be done. The pipes segments to be joined should be preheated uniformly. Preheated copper dissipates heat slowly after welding and reduces the risk of cracking. Depending on the thickness, copper is preheated from 50°-752° Fahrenheit or 10°-400° Celsius.
2) The Welding Process
Before welding, the copper workpieces—copper pipe and copper fittings that must be joined—are assembled. When the desired preheating temperature is achieved, the weld is initiated by producing a molten puddle where the filler is introduced. The filler wire should be introduced as soon as the puddle appears and must proceed around the pipe where the joint is being made. It is important to move fast for welding in a less desirable speed can invite oxidation and can ruin the welding job.
3) Proper Use of Heat and Gas
As a general rule, when TIG welding copper less than 0.01 inch or 2mm thick, Argon should be used as a shielding gas with around 160 amps of current. However, as the copper pipe’s thickness increases, the current should likewise be increased proportionally. For example, in welding copper with thickness of 5mm (0.196 inch), TIG welding requires a preheating of 50°C, as well as shielding gas of argon/helium, and mix up to 300 amps of power; whereas MIG welding requires a preheating of 10-100°C and up to 240 amps of power with argon as its shielding gas.
Whether you are using TIG or MiG welding, if the welding is less desirable, it is advisable to use pure helium as shielding gas. 100% helium shielding gas provides better heat levels that result in faster welding process and better weld quality than that of using argon.
4) Safety
Welding jobs do not only deal with heat, but also with electricity and occasional obnoxious, toxic gases. Therefore, safety is of foremost importance, especially, when welding non-ferrous metals like copper. Lastly, TIG and MIG welders should wear appropriate safety equipment like safety garments, leather gloves, headgear, eye protection as well as respirator mask.