June 11, 2021
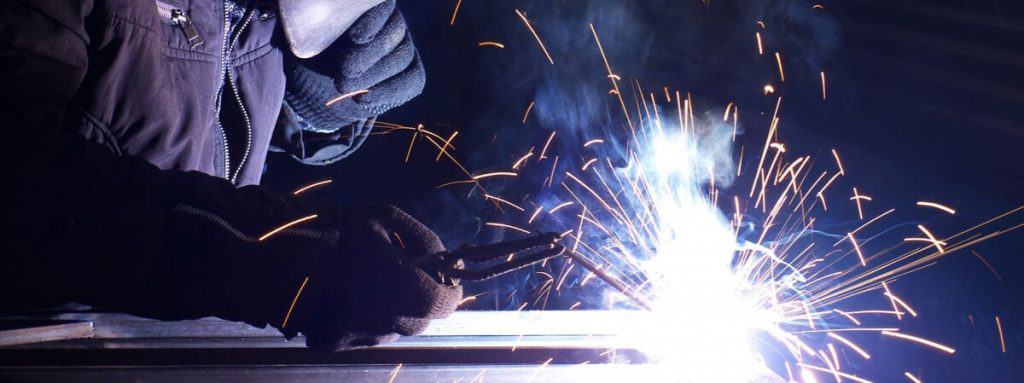
Welding is a process of joining or bonding similar materials (e.g., metals, glass, and plastics) together using fusion. Fusion, on the other hand, is achieved by melting the base materials to be joined. Moreover, a filler material is typically added to the molten materials (weld pools) during the welding process, and these weld pools cool down to form stronger material than the base material itself. Due to this welding property, welding has become the most popular steel-bonding method in construction, shipbuilding, and other industrial applications.
At present, arc welding is the most widely used welding procedure, and as technology advances, arc welding procedures have evolved various techniques. There are several welding processes that are currently in use all over the world. However, this article only tackles the following top five arc welding processes that are presently used for fusing metals.
1) Stick /Shielded Metal Arc Welding (SMAW)
Shielded-Metal Arc Welding (SMAW), otherwise known as “stick” welding, is a welding process that is characterized by the use of a tool known as the welding rod or electrode “stick” that is held by a spring-loaded holder. This electrode carries the electric current to the base material and creates the weld. This welding rod consists of a metal rod covered with a coarse material called flux.
During the welding process, an electrical arc is produced in the gap between the electrode and the base material. The temperature of this arc can reach up to 6,500° Fahrenheit and can melt both the base material and electrode that eventually creates a weld. During this process, the molten pool is shielded from the atmosphere by CO2 gas from the vaporized flux. Hence, a covering material called slag, a byproduct of melting, is created on top of the molten weld pool. This slag is then removed when the weld has sufficiently cooled down.
SMAW is a widely used welding process for it makes use of welding equipment that is very portable and is cheap. Likewise, it can be operated outdoor and is unaffected by rain or wind. Moreover, stick welding can be readily used to weld rusted iron or steel. Due to its ruggedness, stick welding has quickly become a popular construction method and is widely used in steel erection, pipe laying, and building construction.
2) Gas Metal Arc Welding/Metal Inert Gas (GMAW/MIG) Welding
Gas Metal Arc Welding (GMAW) works similarly like that of SMAW. It is a method wherein an electrical arc is created between the base material and electrode. While SMAW’s electrode is composed of short rods, the GMAW makes use of a continuous “wire” electrode that is automatically fed to the welding gun or torch along with the shielding gas at a user-defined speed and pressure. Like the SMAW’s welding rod, the GMAW or MIG welding’s consumable electrode also acts as a filler. GMAW is achieved therefore when the positively-charged continuous wire electrode comes into close contact with the negatively-charged electrode which is the base material. GMAW is mostly utilized for industrial purposes, and it can be used to join a wide assortment of metals. Moreover, GMAW’s electrical source can either be direct or alternating current.
As in any other arc welding type, the area being welded is shielded from the atmosphere using an inert gas that is fed directly to the welded area. Argon gas is the most commonly used shielding agent in MIG welding and is compatible with different base materials such as aluminum, copper, magnesium, nickel, titanium, and its respective alloys. Inert Argon and active oxygen (1-2%) mixture are used to shield the MIG weld on stainless steel; while CO2 gas is used for welding low carbon steel and alloys. GMAW is mostly employed in small to large scale fabrications such as auto body production.
Modes of MIG’s Metal Transfer
For each type of metal, MIG welding uses a variety of shielding gas and metal transfer modes. The metal transfer is the process by which the molten filler material is transferred from the positively-charged electrode to the welded base material. There are three major modes of metal transfer used in MIG welding, and these are the following:
1) Spray Transfer Method
Spray transfer method uses a rapid transfer of electrode metal through stable voltage electric arc to the base material resulting in a clean, high-quality weld line. An increase in the voltage and current values results in a vaporized stream of the filler metal from the electrode. A variation of this metal transfer, which is aptly named Pulsed-Spray mode, uses the pulsing current to melt the filler wire. This melting of filler wire creates a molten droplet of filler that falls on the base material every pulse.
2) Globular Metal Transfer Method
The globular metal transfer is the most cost-efficient method for it uses the less expensive CO2 gas as its shielding agent, and it has high welding speeds of up to 110mm/seconds. During the welding process, a largely molten globule builds up at the end of the electrode and falls to the base material either because of gravity or short circuit that readily creates a blob of filler material.
3) Short-circuiting Transfer Method
The short-circuiting transfer is very similar to globular metal transfer as it creates a molten droplet at the end of the electrode. However, instead of falling into the base material or work piece, the molten filler bridges the gap between the electrode and the workpiece that momentarily short-circuits and extinguishes the arc.
3) Gas Tungsten Arc Welding/Tungsten Inert Gas (GTAW/TIG)
Gas Tungsten Arc Welding (GTAW) is very similar to GMAW welding process, and both use external shielding agent to protect the welding arc from atmospheric effects. However, while GMAW uses a consumable filler wire/electrode, GTAW makes use of a non-consumable tungsten electrode. GTAW or Tungsten Inert Gas (TIG) welding can be employed to create a joint between the base materials with or without filler material.
During the TIG welding process, the tungsten electrode heats up the base material and creates a molten weld pool. This molten pool is protected from the atmosphere by the inert gas like those of argon or CO2 gas that oozes out from the torch’s nozzle. The filler is only introduced to the weld pool to create weld bead that increases the strength of the bond.
GTAW is difficult to achieve manually, and it usually requires a highly skilled or trained operator to achieve a good welding job. This is because the TIG operator needs both hands to perform a TIG weld: one hand is needed to hold the welding head that houses the tungsten electrode and gas nozzle; while the other hand is used to hold, introduce, and withdraw the filler wire to the molten pool. The welder needs to withdraw the torch while the filler is introduced; moreover, the welder needs to withdraw the filler wire when the torch is moved forward.
TIG welding is usually used to join stainless steel, aluminum, copper and magnesium alloys. TIG welding is also widely used for industrial applications like in aerospace industries. Lastly, TIG welding creates high-quality and spatter-free welds and can be used to join thin metal sections.
4) Flux-Cored Arc Welding (FCAW)
Flux-Cored Arc Welding or FCAW is very similar to MIG welding in the sense that both systems require a constant voltage or constant current power supply to create the electrical arc as well as it requires a continuously-fed electrode/filler. However, in FCAW, the electrode/filler is made of a continuous tubular wire electrode with flux filling in its core. The flux in the electrode is enough to shield the molten weld pool from the atmosphere during the welding operation. This method is called the self-shielded method. This process is also somewhat similar to SMAW except that the self-shielded FCAW’s flux is located inside a tubular wire, while in SMAW, a flux-encrusted solid rod is used. This method can be employed outdoors in the same manner as that of the SMAW.
A second FCAW process called dual-shielded method introduces a shielding gas like argon or CO2 gas from an external source. This method is likened to the combination of GMAW/MIG and FCAW welding. Due to the use of gas shielding, dual-shielded FCAW welding method can be readily performed indoors.
5) Plasma Arc Welding (PAW)
Plasma Arc Welding or PAW is an arc welding system that uses electrically-conductive plasma to convey the electrical arc from the negatively-charged electrode to the surface of the workpiece. Plasma is a temporary state of ionized gas achieved by passing through an electric current. Due to the extremely very high temperature (±28,000°C) that it can achieve, PAW system is also used for cutting carbon steel and non-ferrous metals.
There are two basic types of plasma welding process, namely, the transferred and the non-transferred arc process. Both processes utilize a negatively-charged non-consumable tungsten electrode. The stark difference between the two is that, in the former, the arc is formed between the electrode and the positively-charged workpiece, whereas in the latter, the arc is formed between the electrode and the positively-charged constricting nozzle, and the resultant arc plasma is spewed from the nozzle in the form of flame.
For atmospheric shielding, PAW employs either inert gas (Argon or Helium) or Argon and Hydrogen or Helium mixture. Lastly, all types of arc welding are basically partially-ionized plasma; however, PAW’s plasma is a constricted arc plasma.