June 11, 2021
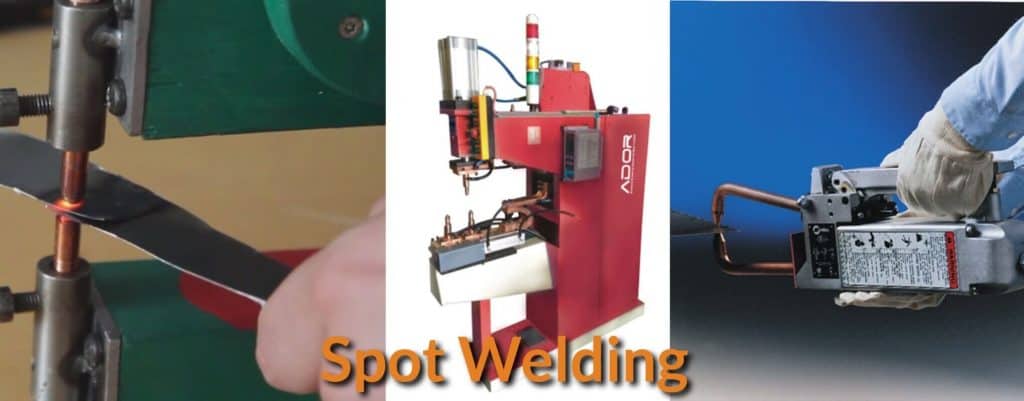
Spot welding is made more accessible by using steel, as the electrical resistivity is higher and thermal conductivity is lower when we compare it to copper electrodes.
What is Spot Welding?
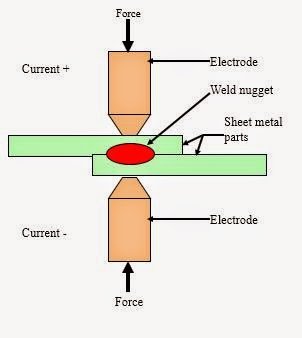
Resistance spot welding is the joining or welding of overlapping metal pieces at small points by applying electric current and pressure. It is a subtype of electric resistance welding wherein the welding process happens via the application of pressure exerted by electrodes and the electric current on the workpieces.
In resistance spot welding, the metal surface points—usually sheets of 0.5 to 3 mm thickness—are pieced together under tremendous pressure exerted by the electrodes. These electrodes are usually made of copper alloy and are capable of concentrating welding current onto the small spots or points while simultaneously clamping the metal sheets together. By pushing a large amount of current onto the target points, the targeted spots are melted and eventually form welds.
Greatest Features of Using Spot Welding
The interesting feature of spot welding is that it can deliver a huge amount of energy to the targeted spot at a very short time of 10 to 100 milliseconds. With this very short time of energy delivery, overheating of adjacent parts of the sheet can be completely prevented. The duration and strength of the applied current and the resistance between the two electrodes generally determine the amount of heat energy that could be delivered to the specific spot.
Professional spot welders generally take into consideration the types of electrodes, properties of materials, and the thickness of the sheets when determining the amount of heat to be applied to the targeted spot. Too much heat will readily melt the parts adjacent to the spot, while too little heat will surely not melt the metal or may result into the poor weld. Spot weld, therefore, necessitates perfect control of the amount of energy to be delivered onto the specific spot.
Metal Materials That Are Suitable for Spot Welding
- Low Carbon Steel
- Aluminum
- Galvanized Steel (More Specialized & Different Spot Welding Method)
- Nickel Alloys
- Titanium
- Stainless Steels
- Copper
The most suitable element for spot welding is low carbon steel. If the alloy steel or carbon content is higher, then there is a possibility that welds could become brittle, which can lead to cracking.
Aluminum can also be used for spot welding, as the melting point is much lower, although it has electrical resistivity and thermal conductivity, which is comparable to that of Copper. But since the resistance of Aluminum is lower, therefore excessive levels of the current need to be used when welding Aluminum. When compared with the steel of equivalent thickness, it is two or three times higher. It is hard to achieve stable, high-quality welding in case of aluminum welding as Aluminum degrades the surface copper electrodes within a small number of welds. Therefore, in the industry, only specialist applications of spot welding can be found. But various new technological developments are emerging to stable good quality spot welding in Aluminum.
Steel coated with Zinc to prevent corrosion, also known as Galvanized Steel follows a different approach than uncoated steel. Since the melting point of Zinc is lower, a pulse of current before welding can accomplish the melting of zinc coating before the steel can join. The Zinc can blend with steel during the weld and lower its resistivity, so to weld galvanized steel, a higher level of current is required.
Nickel Alloys, Titanium and stainless steels (particularly austenitic and ferritic grades) are also common materials for spot welding.
By following resistance spot welding, Copper and its alloys can also join. It is not easy to achieve spot welding with conventional electrodes from copper alloy spot welding, as workpiece and heat generation is the electrodes are alike.
By using an electrode made of an alloy with high electrical resistance and having a melting temperature greater than the melting point of Copper (higher than 1080°C) copper can then be welded. Molybdenum and Tungsten are electrode materials typically used for spot welding copper.
Applications
- Wire Mesh Welding
- Automative Manufacturing Industry
- Spot Welding of Nickel-cadmium
- Metal Sheet Welding (eg: Metal Buckets)
In the welding of particular types of wire mesh, welded wire mesh, or sheet metal, a process called spot welding is used. As the heat flows into the surrounding metal more effortlessly, so it is not easy to spot-weld a thicker stock. It is not difficult to identify spot welding on many sheet metal goods, for example, metal buckets. Spot welding in case of aluminum alloys is possible, but since their electrical conductivity and thermal conductivity is higher, they need higher levels of welding currents. This results in larger welding transformers which are much more expensive and powerful.
In the automobile manufacturing industry, one can find spot welding majorly used. A car frame is created by welding the metal, so it is used almost everywhere. It is easy to automate spot welders, and most of the spot welders found on assembly lines are industrial robots. Painting is the other key application for industrial robots.
We can also find the use of spot welding in the orthodontist’s clinic. In resizing of metal ‘molar bands,’ we can find the use of spot welding equipment, which is small in scale.
Another application of spot welding is in making of batteries, which is done by spot welding of nickel-cadmium, nickel-metal hydride or Lithium-ion battery cells. The cells are linked to battery terminals by spot welding thin nickel straps. Spot welding prevents the battery from becoming extremely hot, as might occur if usual soldering is used.
It is essential to follow good design practices for satisfactory accessibility. It is vital to keep connecting surfaces free of contaminants such as oil, dirt, scale, etc. to ensure that welds are of the highest quality. In determining good welds, the metal thickness is generally not taken into account.
3 Stages in Spot Welding
Spot welding is definitely very effective in joining overlapping sheets of metals, and it is a popular choice among professional welders. The process of spot welding, however, entails three specific stages, namely:
1) Preparation
The preparation process wherein electrodes that are seated on the weld head are positioned towards the spots of the materials to be joined.
2) Heat Transfer
Afterward, a certain amount of current is applied to the workpiece via the electrodes to melt the faying surface of the materials to be joined.
3) Melting Stage
After the contact point has been melted, current is then removed, although the electrodes are left in place to let the material solidify and cool afterward. Professional welders usually allow 0.01 to 0.63 sec weld time, depending on the electrode’s force and diameter and the metal thickness.
The Development of Spot Welding
Spot welding usually necessitates the use of some equipment consisting of the desktop workstation with welding power supply and the electrodes together with the weld head. In the more advanced setup such as in some manufacturing plants, spot welding generally involves automation and robotics.
Pros and Cons of Spot Welding
Spot welding usually necessitates the use of some equipment consisting of the desktop workstation with welding power supply and the electrodes together with the weld head. In the more advanced setup such as in some manufacturing plants, spot welding generally involves automation and robotics.
Advantages of Spot Welding
To figure out whether it is spot welding process that you need, it would be good for you to understand the advantages and disadvantages concomitant with spot welding. Some advantages of spot welding include the following:
- First, spot welding is easy and quick to perform.
- Second, in spot welding, there is no need for filler metal and fluxes.
- It doesn’t make use of dangerous open flame.
- It doesn’t require exemplary expertise.
- It can be performed automatically via the use of automation. In fact, automated machines in many factories usually can perform 200 spot welds within a very short time of six seconds.
- Additionally, spot welding can be performed on many types of metals and can weld dissimilar metals.
- Spot welding can also be easily performed to weld together multiple sheets, and sheets as thin as .25 inch.
Disadvantages of Spot Welding
However, it is also fraught with some disadvantages including the following:
- First, in spot welding, it is necessary that electrodes be properly fitted and are touching both sides of the metals to be joined. However, spot welding machines can only hold metals with certain thickness limitation, and this range of thickness is from 5 to 50 inches.
- Although the electrodes are movable, the electrode holders, however, are only capable of the limited amount of mobility.
- The strength and size of the weld are dependent on the shape and size of the electrodes.
- Spot welding may produce weak and insufficient weld if the current applied is not strong enough or the heat produced is not hot enough.
- Spot welding may produce weak welds if the metal sheets to be joined are not properly held together.
- In some cases, a loss of fatigue strength and warping after finishing the welds usually occur.
- Moreover, the results may be less pleasing if the proper procedures in spot welding are not properly conducted.
- Lastly, the metal and the end-result may come out less resistant to corrosion.
- Spot welding may also create only localized joints that may not be strong enough for the strength of the weld is usually dependent on the applied heat, force, purity, and cleanliness of the metal and electrodes.
- Moreover, spot welding may be quite difficult to use on irregularly-shaped metal pieces. However, the use of portable spot welder can facilitate the process of welding oddly-shaped pieces of metals, for the portable spot welder has electrodes that are conveniently attached to cables to facilitate welding along difficult-to-reach spots.
Caveats to Take Heed of when Spot welding
It is always important to bear in mind that in spot welding, timing is critical in producing great welds. The proper amount of heat and adequate pressure are necessary to achieve optimal results.
Additionally, the correct timing—when applying current and heat to the spot to be welded—would surely play a critical role in producing optimal results. Lastly, it is also important to note that this timing is usually dependent on the thickness and types of metals that are being welded.