June 11, 2021
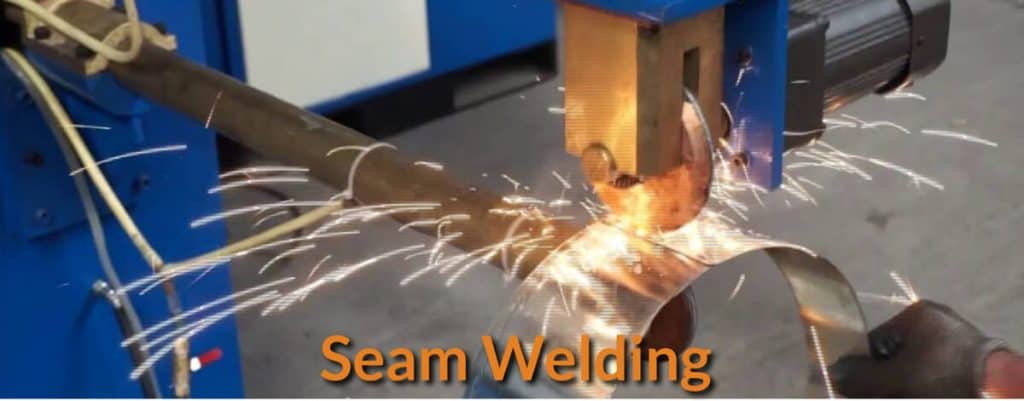
Seam Welding or Resistance Seam Welding is a welding procedure in which a weld is produced in the chafing or fraying surfaces of two chemically similar metals. This welding process is surely different from butt welding, but it can produce lap and butt joints likewise. In seam welding, for example, the welds are slowly yet progressively formed beginning at one end towards to the other end; while in the butt welding, the welder immediately and completely welds the joints at the same time.
Seam welding is somewhat similar to spot welding, and they are both categorized under the electric resistance welding type. They have similarities because they both make use of two electrodes—typically made of copper—for the needed current and pressure. These electrodes are usually disc-shaped and can rotate while the material passes between them. This design makes it possible for the electrodes to be in continuous contact with the material in order to produce consistent and continuous welds. This design likewise allows for easy movement of the materials.
Understanding the Seam Welding Process
Just like any other type of welding, seam welding works with the help of a transformer that provides the needed energy for welding joint. The transformer provides low voltage and high current AC power to actualize the welding process. The joint is heated up to its melting point by the continuous flow of the current. It is necessary for the joint to have high electrical resistance to ensure perfect seamless welding. Once the joint reaches its melting point, the semi-molten surfaces are then pressed together via the aid of the welding pressure to create fusion bond. This results into a seam-like welded structure that is characterized by uniformity. The heat generated by the seam welding process may be so intense; hence, seam welders usually make use of water cooling process to cool down the electrode, controller assemblies, and the transformer.
The end-results of seam welding is definitely very durable, considering that the weld is done under extreme heat and applicable pressure. In fact, if you do it right, the end-result would be much stronger than the material out of which the weld was formed. In the past, seam welding had been utilized to manufacture steel beverage cans. At present, however, seam welding is used in manufacturing rectangular or round steel tubing.
Another distinct characteristic of resistance seam welding is that its electrodes are powered by motor-driven wheels in contradistinction to that of the stationary rods. This mechanism produces non-hermetic seam weld (rolling resistance weld), and this mechanism is highly applicable in joining sheets of metals.
Different Types of Seam Welding
Seam welding can be grouped into two classifications, namely, continuous and intermittent modes. The continuous seam welding allows for an uninterrupted rolling of the wheels to create a consistent and continuous weld. On the other hand, intermittent seam welding creates non-continuous welds along the faying surface. This is achieved by moving the wheels to a specific position and stopping them to make a weld.
There are also three types of seam welding, namely: Mash or Continuous Motion Seam Welding, Standard Seam Welding, Intermittent Motion Seam.
1. The Mash or Continuous Motion Seam
The continuous motion seam welding is made possible by rotating the electrodes at a consistent and predetermined speed to create overlapping weld. This type of welding necessitates timed current impulses to create overlapping weld. It can also be achieved by moving the workpieces at constant speed in between the electrodes under constant welding pressure.
Moreover, in mash seam welding (RSEW-MS), sheets are arranged with small overlap (of around twice the thickness) of the sheet over the other. Afterwards, the sheets are mashed together via the application of current. The end-result is a solid-state joint. Moreover, the welded joint is usually 10 to 50 percent thicker than the sheet. Welders generally engage in post-weld planishing to decrease the thickness of the joint.
2. Standard Seam Welding
The standard seam welding produces welds that are continuous and leak-proofed. These resultant uninterrupted welds are usually achieved by rotating carefully the wheel electrodes on the workpieces and utilizing continuous pulses of currents.
3. Intermittent Motion or Spot Seam Welding
In this type of welding, the pulses of current are supplied intermittently while the wheels move along the workpieces. These intermittent pulses of current, together with the pressure provided by the wheels, create separate spot welds, and these spot welds are not leak-tight joint. Additionally, this intermittent method allows the workpieces to automatically move from one weld position to another weld position. This method is specifically applicable for use in materials that are made of thicker sheets and are resistant to continuous motion method.
Seam Welding and Spot Welding Compared
Seam welding and spot welding are somewhat similar in the sense that both types of welding fall under the category of resistance welding. Because of this commonality, some pro welders believe that resistance seam welding is simply a variation of the resistance spot welding. Spot welding, however, produced weld nugget by simply passing the electric current on the sheet materials that must be welded while being held by shaped copper electrodes. The point—where the surfaces come in contact with each other—receives the highest temperature, and it is at this point where fusion happens. On the other hand, seam welding produces overlapping nuggets. These overlapping nuggets are created by replacing the spot welding electrodes with wheels that readily turn as the materials are passed through the them. This replacement allows for leak-tight seam.
The principle behind the effectiveness of seam and spot welding are basically the same, saved for the fact that seam welding makes use of disc-shaped electrodes. Impulses of current are applied on the rollers, and these current impulses are then channeled by the rollers to the material being welded. With the help of the pressure produced by the electrodes, the seam welding process is then completed. Pro welders can intermittently turn on and off the current to create overlapping nuggets, and this type of welding is aptly termed “Stitch Welding Process.”
The disc shaped electrodes, in the case of seam welding, are not separated during the welding process, and the continuous pressure exerted by these electrodes creates the seam-tight weld. Moreover, the flow of the current onto the electrode is usually timed to produce continuous rows of welds. However, to keep the heat at a minimum level, the electrodes of the seam welding system are generally made of copper alloy.
Seam Welding Applications
Seam welding is a technique of welding in which an electric current is supplied to join two dissimilar or similar metals, and in the process, the formation of a nugget takes place. Usually, the nuggets form in the shape of overlapping welding components or butt.
Seam welding is specifically applicable and preferred over other types of welding, especially, in the following case:
- If you are going to manufacture seam-welded tubing and pipes.
- If you are going to fabricate gas or liquid tight sheets of metal vessels including those of the automobile muffler heat exchangers and gasoline tanks.
- The most important application of role welding is in the manufacturing of almost any type of exhaust system or all types of barrels.
- If you are going to fabricate gas or liquid tight sheets of metal vessels including those of the automobile muffler heat exchangers and gasoline tanks.
- It also finds its use in the manufacture of refrigerators, aircraft tanks, transformers, etc.
- For the welding of nickel alloys, magnesium alloys, and stainless steels is also used.
Pros and Cons of Using Seam Welding
Seam welding is highly popular because it offers the following advantages:
- First, it efficiently utilizes energy.
- It is ideal for making gas or liquid-tight vessels and containers.
- It is better than roll welding because it can produce liquid-tight and gas-tight joints.
- Lastly, it does not require the use of filler metals, and for this reason, it does not produce pollution.
Seam welding is not without its concomitant disadvantages such as the following:
- The use of seam welding is not applicable to metals with thickness that is greater than 3mm.
- The performance of seam welding requires elaborate and complex control system to ensure that the electrodes’ ravel speed is properly regulated.
- Seam welding also requires greater amount of current as compared to spot welding.
- Lastly, the sheets are meticulously overlapped to ensure that there would be no overflow of melted metal.
Precautions for Seam Welding
Many precautions must be taken care of while performing any welding process. It is also true for Seam welding. One of the most important precautions that should be kept in mind while performing seam welding is:
While performing seam welding, take care of the supplied current. If the level of the current provided is very high, then the interface between the roller and welding plates will be extremely hot. In these conditions, it will be challenging to carry out proper seam welding. The welding speed also needs to be kept in mind while performing this process.
To increase the effectiveness of seam welding, at times the weld part is cleaned with water so that during the process, roller type electrodes will remain cool.