June 23, 2020
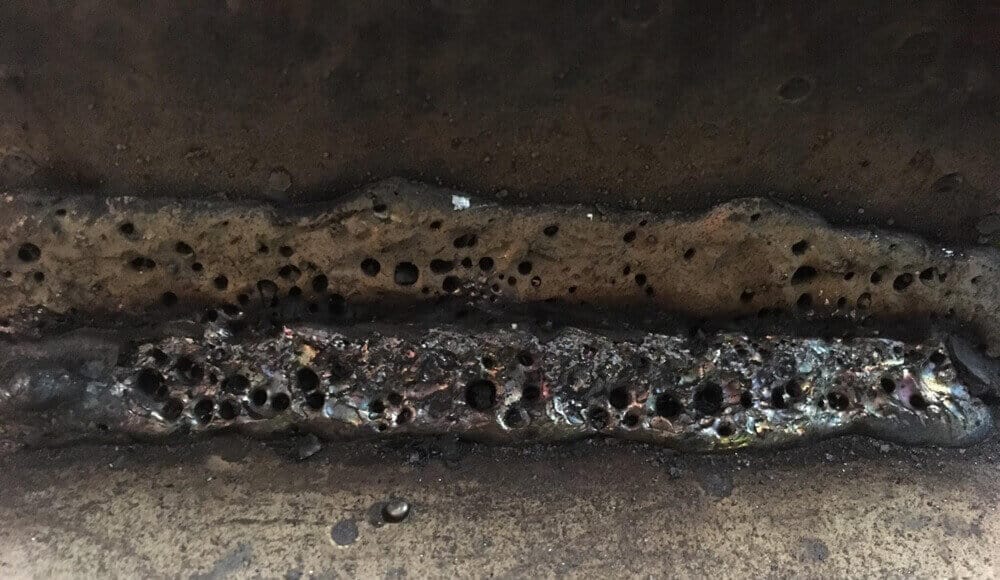
Welding porosity is tiny gas cavities or holes which present themselves in the weld bead. The gas cavities differ in size and are present all around the weld bed in a separate way. They usually present themselves under or on top of the weld surface.
The porosity usually isn’t a problem when it comes to the strength of the weld, except the weld itself is porous. Microscopic sized sequential porosity is sometimes beneficial in some service conditions. Porosity in metal welding is arranged according to their site of appearance and shape.
The gas holes are sometimes shaped like a sphere or extended wormholes that present all over the weld metal.
When it comes to the appearance, holes on the surface of the weld bed are not suitable and could lead to cracks or other defects, thereby making the weld weak. Welding mistakes that are similar to porosity are gas pockets, blowholes, and slag inclusions. They have more of an adverse effect on the weld than the primary porosity.
Possible Porosity-Related Problems
The cylinder has run out of gas. This is the most common cause.
Air or breeze from somewhere prevents the shielding gas from being delivered during welding. A ceiling fan or even a floor fan can prevent the gas delivery. The welder has to be careful of any open door or air produced by any machine. If the breeze moves at about 4 to 5 miles per hour, it could have an adverse effect on the shielded metal arc welding (SMAW) and the flux-cored arc welding (FCAW).
If there is any moisture present, it could also lead to problems. It could just be dew or water, and it could also be condensed liquid resulting from the welding of lap joints or heavy plate, this might occur when the temperature goes below 50 degrees Fahrenheit. To fix this and evaporate the moisture, just preheat the metal to 200 to 220 degrees Fahrenheit.
If the nozzle of the gas metal arc welding (GMAW) is blocked or plugged, most likely from weld splash, this could prevent the shielding gas delivery system. To correct this issue, always check if the nozzle is blocked before you start welding. Double-checking the nozzle could stop weld spatter from entering the weld.
If the weld nozzle is held far from the weld puddle, then there will be a limited amount of shielding gas reaching the weld, which could diminish the weld and also dilute the shielding gas if the atmosphere interacts with the weld.
Causes and Solutions for Most Common Porosity in Welding
Too High Gas Flow
Cause: Turbulence is formed when there is a high flow of gas during welding. The turbulence takes in air, which then reacts with the weld metal resulting in porosity. Before use, check the gas hose for holes or any loose fittings. Inspect the gas cylinders and also the power source/gun or welding torch. If there are holes in the gas hose, then sir can enter, which will cause porosity in the weld.
Cure: make sure you always check and optimize the flow meters before each use. The correct flow and pressure of the gas will prevent external air from interacting with the shielding of the weld.
In-Appropriate Flux
Cause: some materials such as the welding flux, filler rod, base metal, powders, and electrode wires usually absorb moisture quite quickly from their surroundings. This absorbed moisture may be the cause of welding defects. Porosity is also caused by the application of low activity flux.
Cure: ensure that the filler rod, welding flux, powders, electrode wires, and base metal are free of any moisture and kept in a dry place to avoid weld defects. To ensure a high-quality weld without any defects and porosity, then use fluxes with high activity.
Incorrect Surface Treatment
Cause: If the surface of the metal is exposed to harsh chemical paint like zinc coating or treatment, it may lead to porosity. Galvanizing gives off a gas that has adverse effects, which could lead to changes in the procedure and weld parameters.
Cure: the reactions should be predicted long before so as to avoid the defect. Use dry electrodes (use E6010 electrode) for the electrode wires and joints, use EXX15-16 electrodes for the base metal.
Improper Welding Procedure
Cause: If the welding parameters are not adequately set before welding, then this could lead to porosity. Poorly set WPS in the machine and procedure could easily cause defects.
Cure: The welding procedure settings must be set appropriately for every job before welding can start. Check the machine’s welding parameters way before use. Calibrate the machine’s voltage and current readings on the display board before each use.
General Prevention of Porosity When Welding
Use Porosity-free base Metal
Ensure you get a base metal that is porosity free. Avoid getting steel that is high in phosphorus, sulfur, and silicon as they emit toxic gaseous combinations that make gas pockets and blowholes. Also, learn to avoid nonferrous materials that are high in oxygen as they cause porosity in welds. Porosity can also be caused by base metals that have segregations and impurities.
Clean Material Surface
When prepping the material surface, always make sure it is clean as this can significantly improve the welding. Surface contamination and porosity may be caused by the adverse effect of fabrication if not cleaned regularly. This could also cause unstable welds with weak work frames that will need replacement, which causes money and time. To achieve a good weld and prevent contamination in the weld zone. There are wipes produced by Aqua sol. These wipes have concentrated cleaning liquid, which easily removes cutting fluid lubricants, grease, inks, oil, and adhesives.
Monitor The Gas Flow Regularly
Regularly monitor the gas flow from your gas shield. The stronger the flow, the higher the chance of interference, this could lead to impurities in the weld puddle, which could lead to a contaminated weld. Flow rates differ, so it is crucial to choose the right flow rate for every application. This improves the efficiency and results in a high-quality weld. If you do not know what the right flow is, then contact your gas supplier for the information.
Inspect your machine regularly. Due to age, the hoses may develop holes and leak, or the wires may become exposed or torn. Inspect the connections before welding aids a precise amount of flow from the gas shield.
Make Sure The Nozzle Is Always Clean
Inspect the nozzle of the weld gun to ensure that it is clean; due to constant usage, the tip may become blocked, which will lead to the build-up of contaminants in the weld. Regularly inspect your drive rolls or wire spool hub tension. Low-quality wire feed execution is most times caused by weak tension.