June 11, 2021
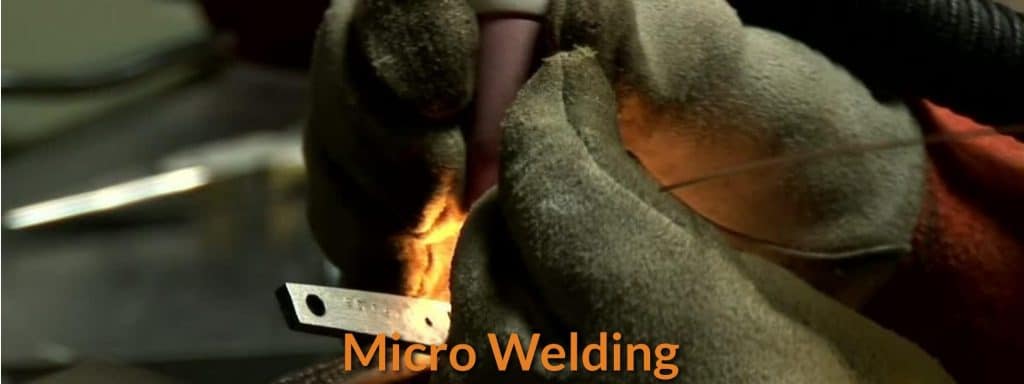
Micro welding is a precision type of welding that is typically designed to join together delicate minute components. It is the process of welding together ferrous and nonferrous metal parts of the minute thickness of less than 0.5 mm with the cross-section of up to 10 sq. mm, and it produces welding beads of .065 up to .005. Moreover, micro welding is considered as a delicate art because of the precision by which it is wrought. As an art, Micro welding is performed on a very small area, and often, it is done with precise heating in order not to affect the adjacent areas, and to allow precise fusion of the joint.
The Process of Micro Welding
Those who are not adept in micro-welding can only imagine how micro-welding is wrought because the process is done on the micro level. A micro welder, for example, must operate on minute wires with .005 mm in diameter. Yet, despite the minuteness of these wires, the joining of these micro wires is precisely done via the use of highly-specialized technologies and equipment. Moreover, since the process is performed on a miniature scale, micro-welding is often wrought under a microscope.
Under the microscope, the depositing of welded metal via the use of minimal heat in a tightly controlled environment can be carefully and meticulously done. Since micro welding necessitates the use of a microscope, it also requires miniature tools and equipment to correctly carry out the placement of filler metal and hardware elements. Additionally, it requires adeptness in the use of miniature tools and equipment which only an expert micro-welder can usually perform with utmost precision. Furthermore, with masterful precision, the micro welder can apply the exact amount of heat energy on the targeted area without affecting the adjacent surroundings.
Different Types of Micro Welding
Micro Welding is usually done via the use of different methods such as those of electric, pressure-contact, electrostatic, ultrasonic, cold, electron-beam, Thermocompression, or laser methods. The following, however, are the four generally-known types of micro welding:
1. Micro Laser Welding
The first type of micro-welding is the micro laser welding. This type of welding utilizes a solid-state fractional laser to perform micro welding. Usable applications or apps are incorporated in this type of micro welding to ensure and to allow for s completely automated procedure for this type of micro welding. With utmost precision, this type of micro welding produces the very best quality of welded joints.
The use of fractional laser for micro welding allows for deep inside welds. Compared with the Electron Beam Welding, this type of micro-welding can be operated with no pressure requirement, since laser, as a form of light, can be operated through the air without necessitating a vacuum chamber. Lastly, Micro Laser Welding is so precise that it produces no contamination, saved for the use of the shielding gas when operating on highly reactive materials.
2. TIG Micro Welding
TIG Micro Welding necessitates the use of minute TIG welding equipment like that of the Gas Tungsten Arc. This tool—although a bit smaller than a pen—can operate with utmost precision. Micro TIG provides the micro-welder with greater control for weld placement, and it also produces fewer residual stress. It likewise allows for greater structural integrity. With the use of the Micro TIG, one can restore damaged components and weld together minute parts even if these parts contain high alloy density.
3. Flash Micro-welding
The Flash Micro-welding type is designed for cost-efficiency and high production. It is utilized for large-diameter steel-rod processing. This type of micro welding consistently produces high-quality welds using heavy upset pressures that are delivered by a motor-driven cam assembly. As a reduced version of butt welding equipment, this type of micro-welding is utilized for welding together, band saw ends and hot junction of various thermocouple wires. If you would scrutinize the different elements of this micro welding machine, you would readily notice that it has the same elements as those of the full-sized machine. However, this reduced version is designed to operate on a micro level. Moreover, this type of micro-welding is engineered to manufacture decorative chains of regular or precious metals and can operate automatically to form fantastic links.
4. Resistance Micro-welding
This type of micro-welding utilizes a miniaturized type of micro-welding equipment to perform seam-resistant or spot welding. It can perform precise micro welding by gripping the different elements that should be welded together in between precisely-built electrodes that could apply exact current and pressure flow during the process. This type of micro-welding likewise can perform precise projection weldings via the use of equipment that is engineered to make use of the located bulges or deformations. This allows for the simplification of the aligning and positioning of the elements that must be welded together.
Conclusion
Experienced welders approach micro-welding works with utmost precision and extreme attention to detail. They select the right equipment, consumables, and processes to facilitate the process of micro welding. Lastly, they follow the proper steps when welding minute parts to ensure that their works are perfectly done.